Company cooperation: Increasing productivity, increasing efficiency
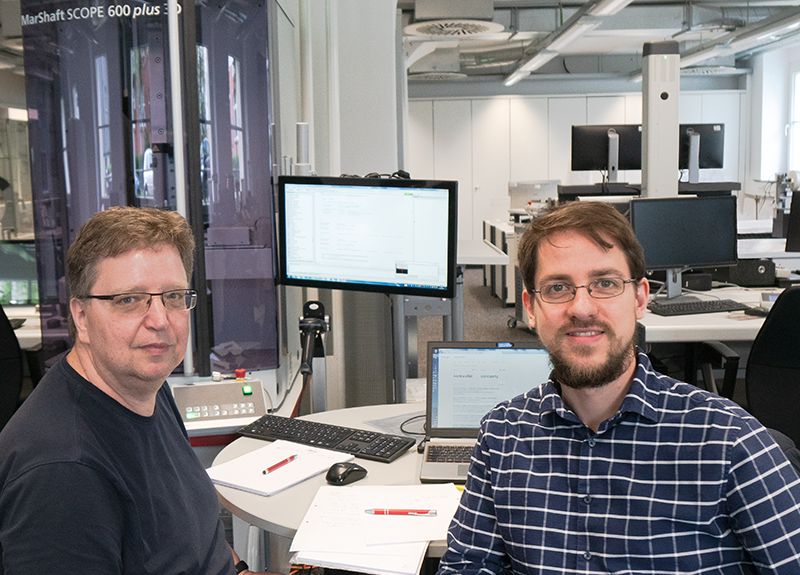
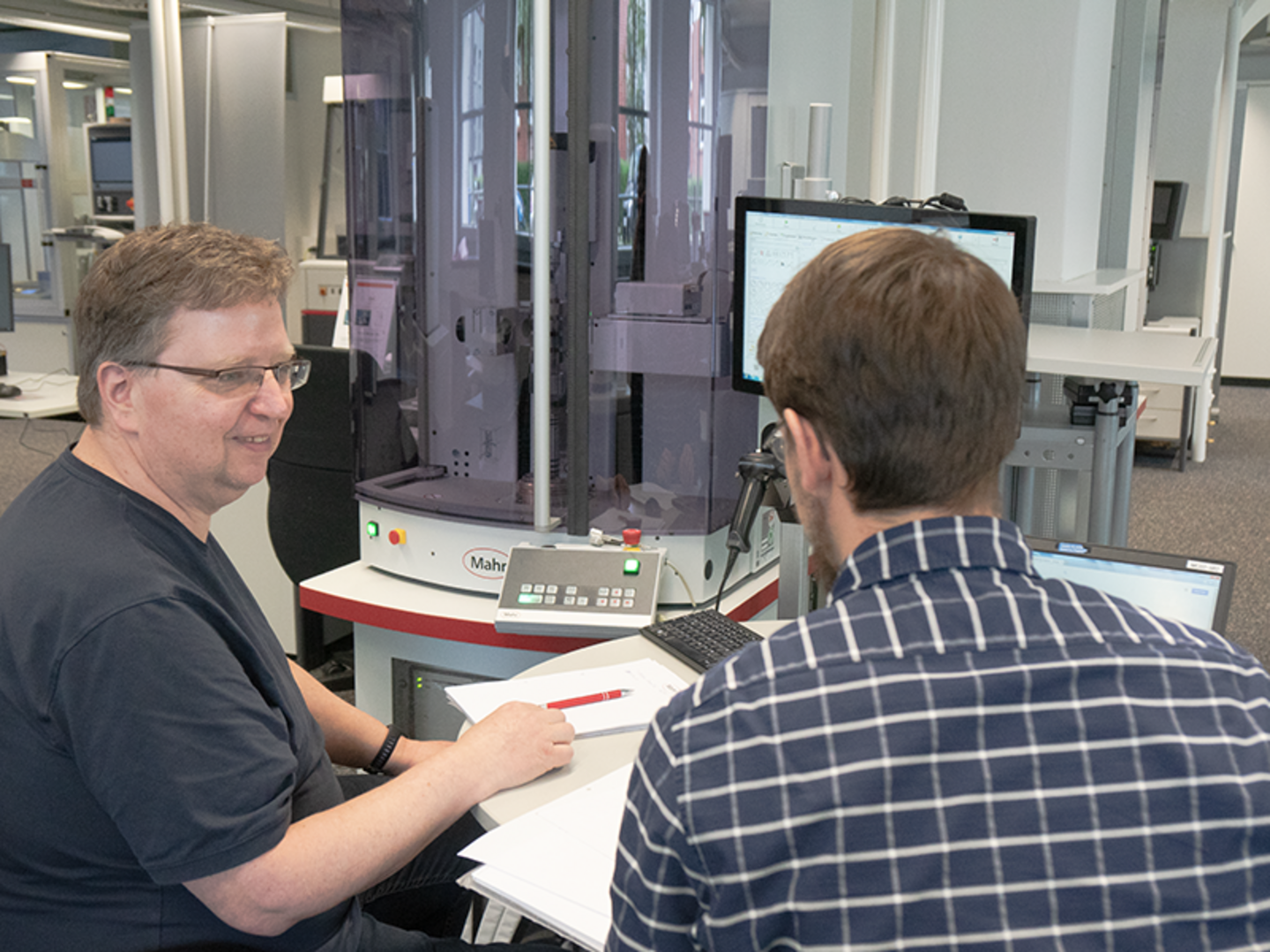
Modern metrology faces enormous challenges with regard to its measurement performance. In cooperation with the company Schleicher Fahrzeugteile GmbH & Co. KG, Mahr is developing a measuring device that combines the existing qualities of several machines.
Modern metrology is in a state of upheaval. Last but not least, the industry trends presented at Control 2019 have shown that increasing productivity is rapidly gaining in importance in industrial production. Results should be available faster and, above all, more efficiently, so that companies can produce more economically and save costs.
Strong partners in honest exchange
The demand is placed on proven metrology to be constantly optimized in order to keep pace with new requirements. As developers of measuring machines, we have set ourselves the goal of advancing these optimizations – and offering our customers exactly what they can expect from modern measuring technology today. In order to meet our own demands and to gain valuable input from our customers, we are pleased to cooperate with Schleicher Fahrzeugteile. As a long-standing business and now also development partner, there is an honest, trusting relationship – an absolute prerequisite for the success of such a cooperation.
The development has begun
The aim of the joint venture is to optimize the measurement software of the existing MarShaft Scope 600 plus 3D for optical and tactile camshaft measurement. This is intended to improve the current functionality, as several measuring instruments have always been used to measure a camshaft. Up to three different measuring devices are required to measure features such as cam shape, bearing diameter, functional bores or geometric shapes, as these features are usually all measured using different methods.
Camshaft measurement with the MarShaft SCOPE 600 plus 3D
Mahr wants to eliminate this problem with the development of the MarShaft SCOPE 600 plus 3D. The new measuring software will combine the individual measuring steps such as contour measurement, form and position measurement and 3D measurement in order to save time and money. This is made possible by the combination of optical and tactile measuring sensors within the device, which makes 3D measurements possible. In this way, a camshaft can be measured in a single fixture, in a single measuring device.
Inspection by the customer – for the customer
Schleicher Fahrzeugteile GmbH assumes the role of inspector in the cooperation. The employees, especially users of shaft metrology in camshaft production, were prepared for their task with on-site user training. At regular status meetings, the experience gained with the Mahr measuring machine is then discussed and technical suggestions given. The knowledge of the practical users helps Mahr to further develop the measuring software and to further optimize the user interface for camshaft manufacturers and their special products on the basis of the employees' experience.
First interim conclusion in April
At the beginning of April 2019, the first interim conclusion was drawn at Schleicher Fahrzeugteile in Penzberg. On this occasion, the Product Manager MarShaft von Mahr, Thomas Köhler, visited the production site together with the responsible application engineer. In a joint maneuver critique, the measurement engineers drew a first, pleasing conclusion: Although the pure measurement time is in the same order of magnitude as the sum of the individual machines, setup time, changeover time, and transport time are eliminated for the operator. This saves them time, which in turn can be used for other purposes.
Second interim conclusion: time saving of 15 minutes
At the beginning of June, Rico Voß, metrologist at Schleicher, visited Mahr again. Together with the Mahr application engineer, Stefan Lüders, a positive course of the development process is emerging: "With the MarShaft SCOPE 600 plus 3D, 15 minutes can now be saved per camshaft thanks to complete measurement in just one set-up – a huge improvement over conventional camshaft measurement technology. The machine is also now fully integrated into the quality assurance process at Schleicher and is used and further tested under real production conditions.