A world first, revolutionary and unique: measuring roughness directly in the processing machine
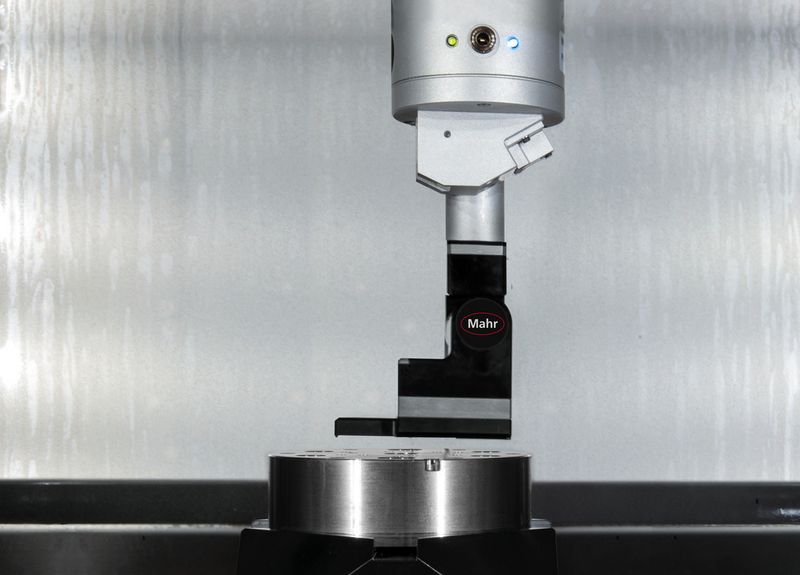
The MarSurf MC 510 is fully integrated into the tool holder so that it can measure directly in the CNC production machine. It measures by means of a vibration-resistant, tactile measuring system – standard-compliant and highly accurate down to Rz 1 µm. It is available quickly and highly productive: if a roughness measurement is required, the machine automatically inserts the measuring device from the tool magazine into the spindle like a regular machining tool without changing the position and clamping of the workpiece. Various tool holders are available as interfaces, including types SK 40 and HSK-A 63. As soon as the measuring device is ready, it can be easily aligned using the software-controlled, flexible swivel joint. The measuring movement is carried out by the integrated feed drive, whereby the CNC machine positions the device at the desired measuring point.
The following video illustrates how the MarSurf MC 510 works:
Advantages that pay off
The integrated roughness measurement offers users a wide range of benefits:
Use the tool longer: Thanks to continuous monitoring during the manufacturing process, the tool can be used until the actual end of its service life as long as it meets the specified surface specifications. This reduces the customer's tool costs by up to 20 percent, as the tool can be changed later.
Save time: Measuring surface roughness directly in the machine eliminates the need for separate measurements. This can lead to a time savings of 30 to 50 percent during quality control.
Reduce costs: Saving time and reducing rejects through early detection of quality problems can reduce quality control costs by an average of 10 to 20 percent.
Optimize processes: Continuous feedback on surface roughness makes it possible to better control the manufacturing process and actively intervene. This reduces machine downtime and, in turn, increases machine utilization byaround 15 percent.
Reduce rejects: More accurate and consistent quality measurements significantly reduce material waste, in some cases by up to 40 percent.
Fully automatic and reliable documentation
The machining processes in the CNC machine remain flexible as the measuring device is controlled directly; the measured values can be called up in the NC code. The MarSurf MC 510 communicates wirelessly with the Edge PC. It also has an OPC UA interface and is closed-loop ready. Finally, the surface parameters are documented fully automatically and securely, with no expert knowledge required.
Ideal for automated production processes
Additional sophisticated features make the MarSurf MC 510 a practical and economical addition to CNC production machines. Thanks to its robust design, it is reliably protected against soiling. Its power supply is independent of the processing machine, as it has a powerful rechargeable battery. The automated process ensures fast measurement of the surface characteristics and precisely reproducible measurements without operator influence. It is also possible to draw conclusions about tool wear, which reduces tool costs. Overall, the device is therefore ideally suited for automated production processes – regardless of the machine and control system. This is because the MarSurf MC 510 offers reproducible measuring conditions without operator influence – reliably, flexibly and efficiently.
Would you like to experience the MarSurf MC 510 live at AMB?
Then get your free trade fair ticket here!