3 consejos profesionales. Así funciona la medición de formas
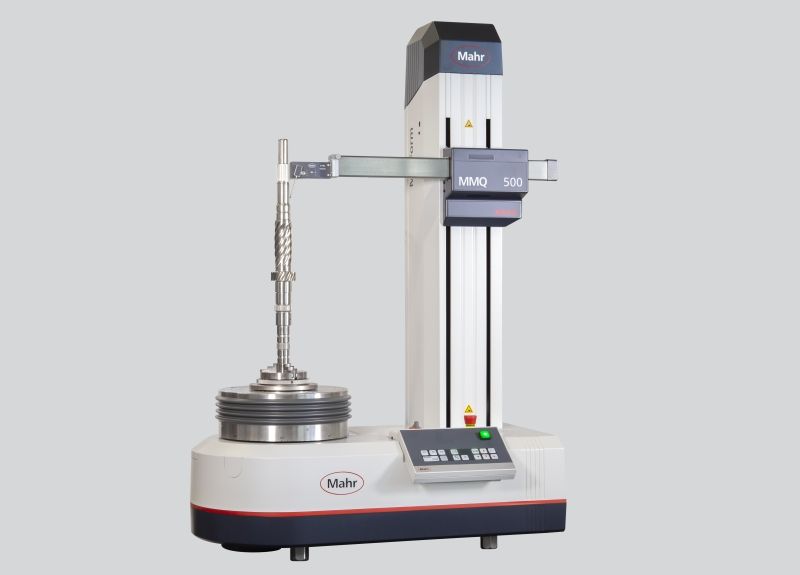
Consejo 1. Aplicar los filtros correctos
Para evaluar correctamente los datos de medición, es fundamental elegir los filtros correctos en el software. No obstante, si ni la norma de la casa ni el cliente proporcionan especificaciones relativas a estos ajustes de filtro, le recomendamos que proceda de la siguiente manera. En primer lugar, decida la tarea de medición que desea realizar con su medidora de formas, a saber, comprobación de la rugosidad de la superficie o medición de formas. Es sencillo. Si desea comprobar la rugosidad de la superficie de una pieza de trabajo, utilice los datos de longitud de onda corta para el análisis y descarte los datos de longitud de onda larga. Al contrario, si lo que desea es realizar una medición de formas, filtre y evalúe los datos de longitud de onda larga relacionados con la forma, pero no los datos de longitud de onda corta.
De todos modos, también existen otras diferencias entre las dos tareas de medición descritas. Para medir la rugosidad de la superficie, los ajustes de filtro se definen en términos de milímetros o pulgadas. Por ejemplo, si establece el filtro a 0,8 mm, esto significa que las desviaciones de superficie de menos de 0,8 mm se aceptan como rugosidad de la superficie, mientras que los elementos de más de 0,8 mm no se incluyen en el resultado.
En cambio, los filtros de forma para las mediciones de redondez, por ejemplo, suelen especificarse como magnitud angular, pero no en grados angulares, sino en lo que se conoce como «ondulaciones por revolución» (UPR, por sus siglas en ingles). Así, muchos usuarios eligen 50 UPR como valor predeterminado, lo que significa que la longitud del arco es de un 50º de círculo o una sección en la superficie de un objeto redondo, lo que corresponde a 7,2 grados. Sin embargo, la longitud del arco cambia de forma análoga al diámetro de la pieza de trabajo.
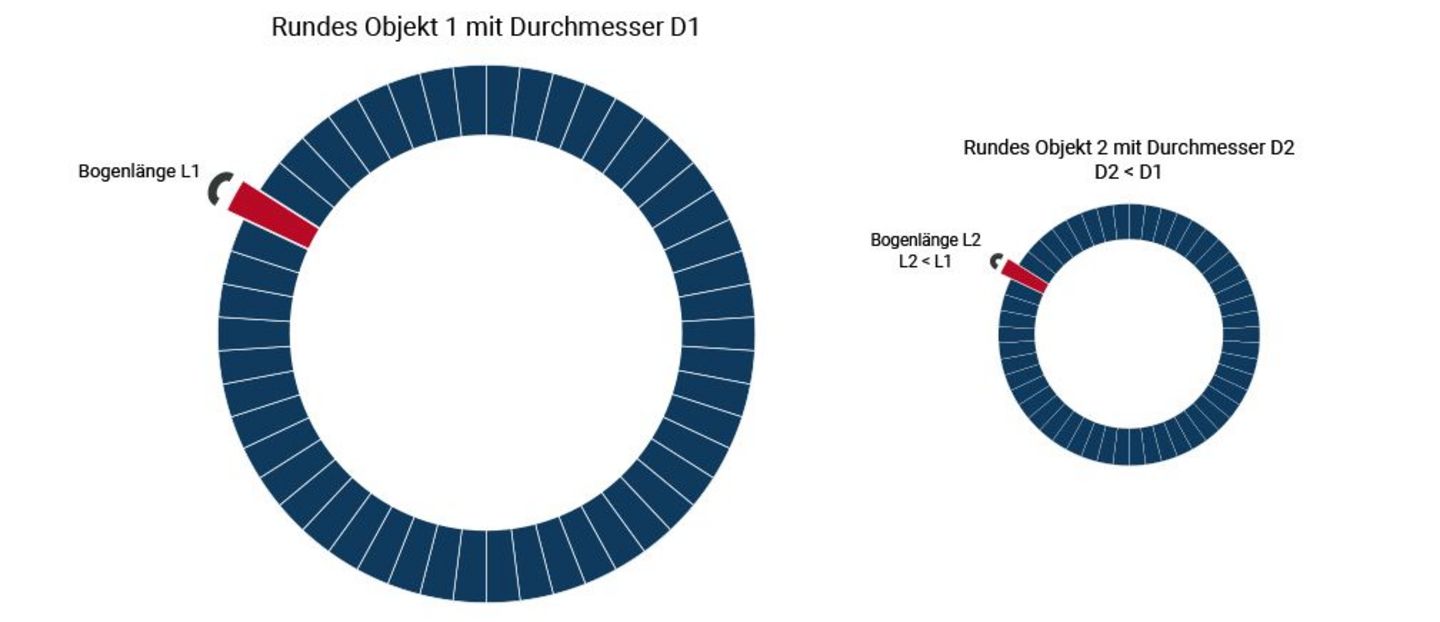
Por lo tanto, siempre es necesario elegir el filtro adecuado en función del diámetro y de la función posterior que tendrá la pieza de trabajo. Dependiendo de la elección del filtro, los defectos de forma pueden contener solo componentes «bastos» (la pieza de trabajo es ovalada o de «igual grosor por tres lados»), o también componentes con características más definidas, como las ondulaciones de una frecuencia más alta.
Puede obtener más consejos sobre la elección correcta del filtro en función del diámetro y de la aplicación de que se trate, por ejemplo, en los cursos de formación de la Mahr Academy, o bien durante una sesión de formación directamente en su medidora de formas Mahr.
Consejo 2. Seleccionar el tamaño correcto del elemento de palpado
A la hora de elegir el elemento de palpado, también hay que tener en cuenta las dimensiones del componente que se va a comprobar. Esto se debe a que la esfera de palpado, como punta del elemento de palpado, es en sí misma un filtro mecánico. Por lo tanto, el elemento de palpado debe corresponder al tamaño de la pieza de trabajo y al número máximo medible de ejes por revolución. Si un elemento de palpado demasiado grande se desplaza por la superficie de medición, no puede sumergirse de forma óptima en todos los valles del perfil real. En consecuencia, el elemento de palpado inadecuado provoca un filtrado mecánico no deseado de los datos, los que falsea los resultados de medición.
Por cierto, la Sociedad de metrología y automatización de la VDI/VDE le asesorará sobre los criterios que deben aplicarse al seleccionar el elemento de palpado correcto. Así, la hoja 3 de la directriz VDI/VDE 2631, relativa a los principios básicos de la metrología de formas, contiene instrucciones relativas al uso del elemento de palpado correcto. La MarForm MMQ 500 permite utilizar cómodamente el elemento de palpado correcto. Su unidad de brazo de palpado aloja hasta cuatro brazos de palpado a la vez y permite un cambio rápido y totalmente automático en función de la tarea de medición y sin intervención del operario.
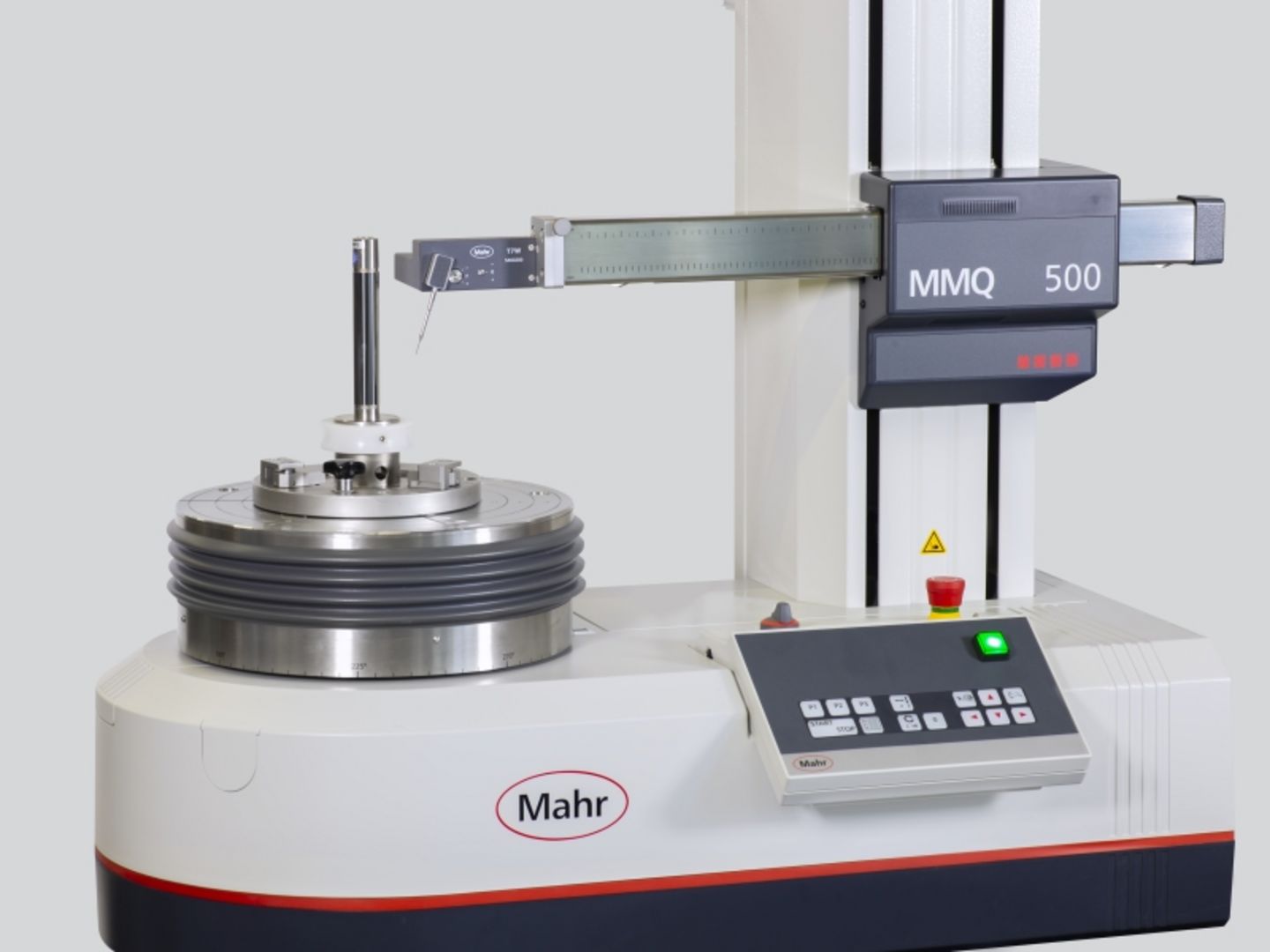
Consejo 3. Alinear eje de la pieza de trabajo de forma exacta
Antes de poder medir las características de forma y posición de una pieza de trabajo con una medidora de formas, es necesario alinearla. Utilice la mesa de centrado y basculado para realizar operaciones de centrado y basculado de manera que el eje de la pieza de trabajo y el eje de rotación de la medidora de formas estén alineados, lo que evitará que se midan supuestos errores de forma que no existen en absoluto. Por ejemplo, en el caso de una mala alineación, un corte a través de un cilindro oblicuo puede aparecer erróneamente como una elipse en lugar de un círculo. Por su parte, una alineación correcta evita que el punto de palpado, que idealmente se encuentra exactamente en el plano X-Z, se desplace durante la medición.
Las medidoras de formas que tienen una mesa de centrado y basculado automática, como ocurre en el caso de la MarForm MMQ 500, permiten controlar muy bien los errores de alineación. Gracias a la alta precisión existente durante la alineación, los errores que se producen en la medición de la redondez son prácticamente inapreciables. Por ejemplo, una excentricidad residual típica de 5 µm para un cilindro con un diámetro exterior de 50 mm da lugar a una desviación de redondez adicional de menos de un nanómetro. Para otras características, en particular, las relativas a la posición, o los componentes con diámetros pequeños, el efecto de los errores de alineación puede ser mayor. Sin embargo, puede mantenerlos en un nivel inapreciable si consigue una alineación exacta.
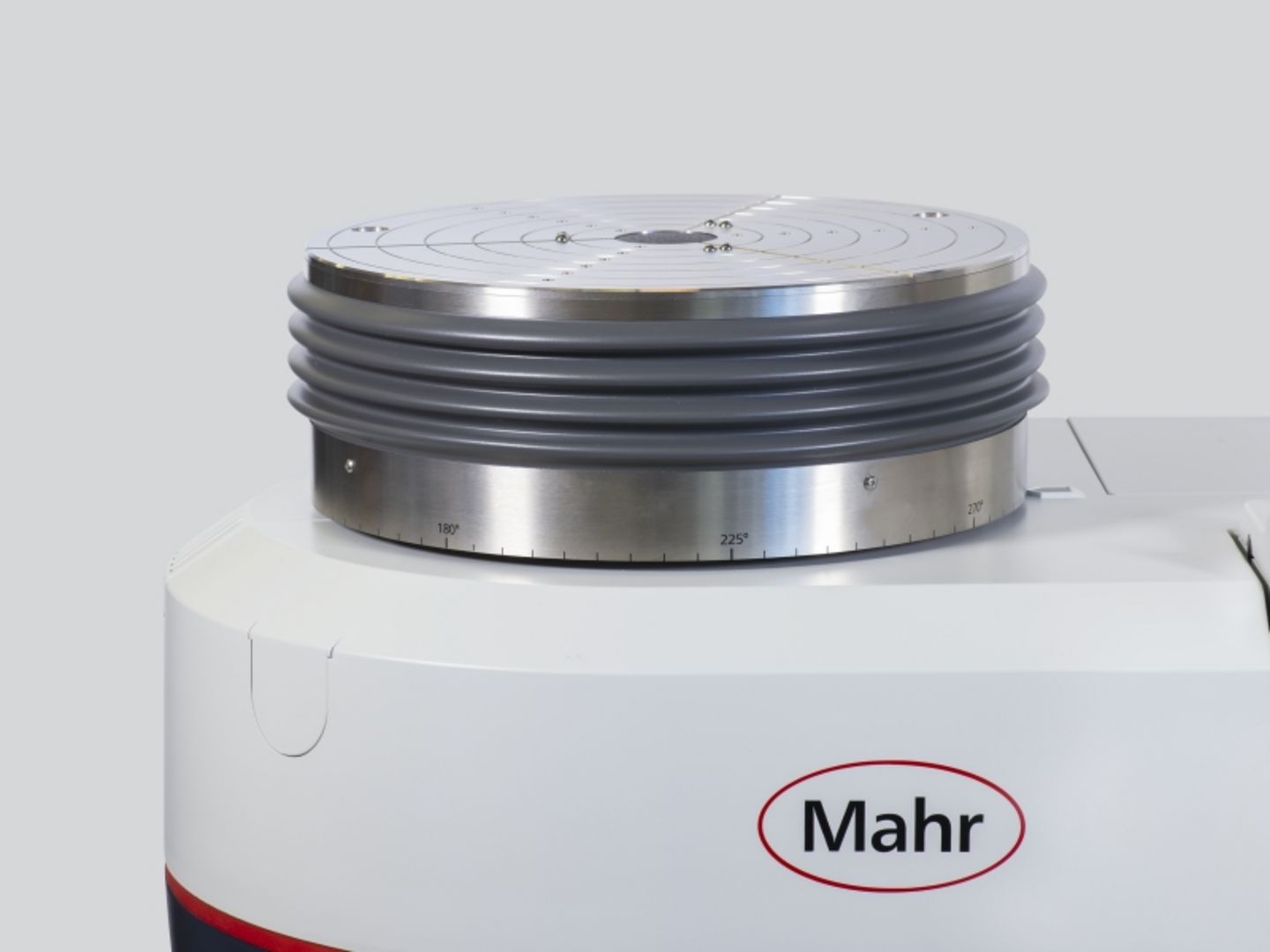
Así pues, en la práctica, existen dos cuestiones fundamentales durante la alineación:
1. ¿Dónde, es decir, en qué puntos de la pieza de trabajo es preciso realizar la alineación?
2. ¿Con qué precisión debe alinearse la pieza de trabajo?
Si una pieza de trabajo tiene una referencia principal, debe alinearla siempre con esta referencia. Si no hay una referencia principal, puede resultar útil realizar la alineación en los puntos con tolerancias más bajas. Se recomienda limitar la inclinación a diez veces el valor numérico de la excentricidad residual (5 µm de excentricidad residual por cada 50 µm/m de inclinación permitida). En ese caso, la inclinación restante no causa ningún problema, independientemente de la distancia entre los círculos medidos.
Para numerosas tareas de medición, la excentricidad residual de 5 µm almacenada como valor predeterminado en el software MarWin es absolutamente suficiente. Las medidoras de formas de Mahr suelen alcanzar este valor de forma rápida y fiable, por lo que, en principio, no debería ser necesario utilizar valores más altos. En el caso de tolerancias bajas (por ejemplo, redondez de 1 µm, cilindricidad de 5 µm o salto radial de 5 µm), así como en componentes con diámetros pequeños (10 mm o menos), se recomienda reducir la excentricidad residual permitida. Con la nueva medidora de formas MarForm MMQ 500, podrá alinear sus componentes de forma fiable y rápida, incluso en los casos de una excentricidad residual extremadamente baja.