Aplicación de la metrología neumática en el caso de aparatos ortopédicos
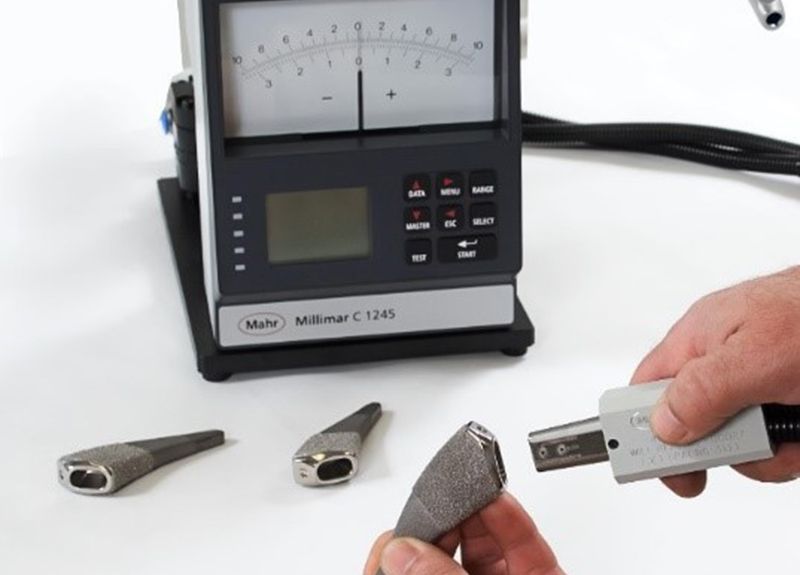
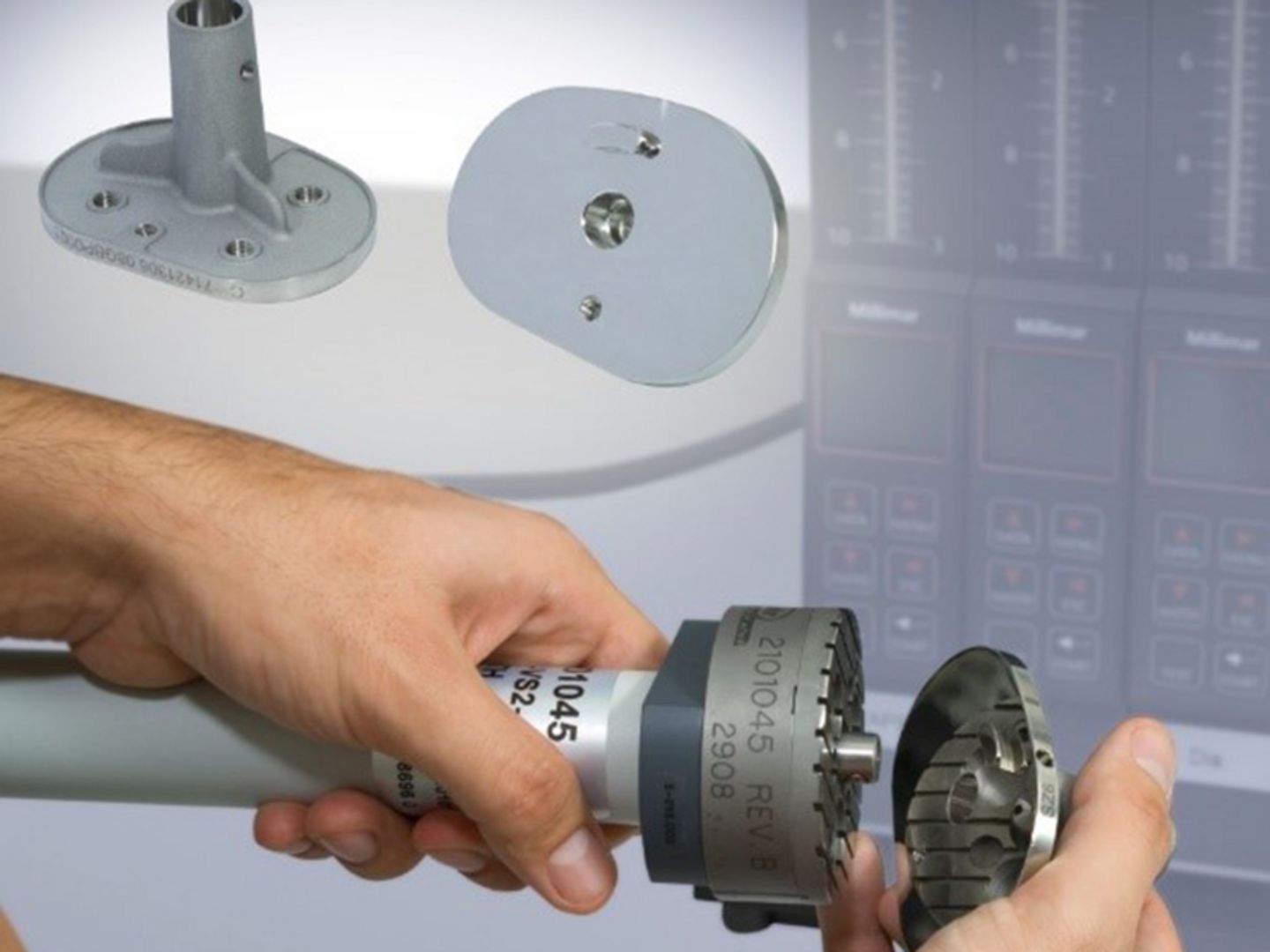
Los componentes ortopédicos de precisión solo pueden cumplir con los exigentes requisitos de calidad si cada paso de producción individual (desde el primer corte hasta el procesamiento final) mantiene una estabilidad constante. Esto requiere una inspección de las características orientada al proceso, así como una retroalimentación inmediata en el caso de que se superen las tolerancias y la documentación adecuada de todos los datos del proceso.
Normalmente, a medida que las piezas de trabajo avanzan en el proceso de fabricación desde la materia prima hasta el producto acabado, las tolerancias dimensionales, la calidad de la superficie y las características geométricas se vuelven cada vez más cruciales, lo que significa que es extremadamente importante mantener estas tolerancias o detectar a tiempo si se han superado. Una de las características dimensionales que se miden al final del proceso de fabricación de aparatos ortopédicos es la estrecha tolerancia en las superficies cónicas para el ajuste de las piezas individuales. Por ejemplo, la mayoría de las prótesis de cadera y rodilla utilizan superficies cónicas para una alineación óptima y un «bloqueo» seguro de los componentes en la posición correcta. Incluso durante la fabricación de estas piezas, el control de la forma y del tamaño del cono determina el rendimiento que tendrán los implantes ortopédicos a lo largo de su vida útil.
¿Por qué la metrología neumática es el método más eficaz?
Con unas tolerancias cada vez más ajustadas, los aparatos de medición deben ser cada vez más robustos y tener las características de diseño adecuadas para garantizar la correcta sujeción de las piezas. Además, también deben tener la resolución y la precisión apropiadas para medir las tolerancias que se necesitan. Por eso, la metrología neumática se ha convertido cada vez más en el instrumento de verificación preferido a la hora de comprobar estos parámetros tan decisivos. Los aparatos de medición neumáticos son extremadamente precisos y ofrecen resoluciones muy altas. Suelen utilizarse para aplicaciones en las que las tolerancias son estrechas, por lo general, inferiores a ±25 µm, y donde la rugosidad de la superficie es inferior a Rz 6,3 µm. Cuando se dan estas condiciones, como ocurre en el caso de los conos de precisión para aplicaciones médicas, la metrología neumática suele ser la mejor solución.
La medición neumática también es especialmente adecuada para comprobar las relaciones dimensionales; los aparatos de medición neumáticos son rápidos, fáciles de manejar y tienen una vida útil de muchos años, incluso en las condiciones de funcionamiento más adversas del área de producción, por lo que permiten medir millones de piezas. En algunos casos, la metrología neumática puede utilizarse incluso para inspeccionar y evaluar las características de forma específicas de una pieza.
La tobera de medición, es decir, esa pequeña abertura por la que sale el aire, es la razón por la que la metrología neumática es tan útil a la hora medir las superficies cónicas de los aparatos ortopédicos. Ningún otro sensor de medición es tan pequeño ni puede colocarse tan cerca del punto de medición cuando es necesario medir varios diámetros o varias formas geométricas. Bien es verdad que los sensores electrónicos o de corrientes de Foucault pequeños pueden acercarse al tamaño de una tobera de medición, pero no pueden igualar su rentabilidad ni su idoneidad para el uso directo en el área de producción del taller.
Los diámetros y los conos pueden medirse mediante una combinación de sensores electrónicos, o bien a través de una máquina de medición de coordenadas (MMC) con palpadores de bordes. La tobera de medición puede instalarse directamente en un aparato de precisión para poder medir la pieza directamente en el área de producción, lo que a su vez permite completar la medición en un proceso rápido con un esfuerzo mínimo por parte del operario. Ni las MMC ni la metrología óptica ofrecen la velocidad ni la precisión necesarias para lograr una inspección del 100 % de las piezas de trabajo que se encuentran en producción y proporcionar información inmediata sobre el rendimiento del proceso.
Selección del diseño correcto del instrumento de verificación
Existen prácticamente tantos métodos para especificar los requisitos de conicidad como fabricantes de componentes cónicos. La zona de referencia puede variar de un fabricante a otro y las tolerancias pueden especificarse de diversas maneras.
Dependiendo de cómo se ensamblen las piezas en una unidad, las tolerancias en el cono pueden ser más estrictas que en los diámetros o viceversa. Otra alternativa consiste en especificar una combinación de tolerancias cónicas en un solo diámetro, lo que implica que los datos que aparecen en el dibujo o plano son la mejor guía para seleccionar el modelo más adecuado del instrumento de medición neumático. En la metrología neumática, los instrumentos de verificación se hacen a la medida para cada aplicación cónica diferente, por lo que es fundamental examinar los requisitos teniendo en cuenta las características específicas de la pieza de trabajo de que se trate. Sin embargo, la flexibilidad y las ventajas de este método de medición son casi insuperables: así, ofrece resoluciones muy altas y los sensores de medición pueden combinarse de muchas maneras para obtener cualquier número de datos de medición dimensional y geométrica directamente en el área de producción.
Diferentes tipos de medidores neumáticos de conos
Los implantes médicos deben ser excepcionalmente duraderos y resistentes, por lo que el ajuste cónico entre la matriz y el macho debe ser extremadamente preciso. Además, las dos piezas deben estar bien conectadas entre sí y a la altura correcta. Durante la fabricación, la práctica habitual es inspeccionar el 100 % de las piezas, pues el objetivo es garantizar la precisión de fabricación de ambos componentes. Esto suele hacerse mediante la metrología neumática diferencial, que combina la alta resolución y precisión necesarias con la rapidez, la facilidad de manejo y la robustez que se exigen en el área de producción.
El tipo más habitual de instrumento de medición de conos neumático presenta dos pares de toberas en dos planos de medición y está diseñado para la pieza de revestimiento entre la pieza de trabajo y el instrumento de medición (consulte las figuras). Si el ángulo del cono es demasiado grande, queda más holgura entre las dos superficies en el extremo más pequeño del cono. Por el contrario, si el ángulo del cono es demasiado pequeño, queda más holgura en el extremo más grande. En cualquier caso, esto puede reducir el arrastre de forma de la conexión, lo que hará que la «conexión segura» se pierda con el tiempo porque se afloje o se gire en exceso. Así, si el ángulo del cono es correcto, pero el tamaño es incorrecto, se producirá una longitud total incorrecta de la unidad ortopédica y, por lo tanto, se obtendrán resultados inesperados después de colocar el implante.
En el caso de los tampones neumáticos cónicos con pieza de revestimiento, no se miden diámetros parciales, sino que la diferencia de diámetro se indica en dos puntos de medición de la pieza de trabajo que, a continuación, se comparan con los puntos de medición correspondientes del patrón o del maestro. Si la diferencia de diámetro en el extremo grande del cono es mayor que la diferencia de diámetro en el extremo pequeño, las toberas superiores detectan más contrapresión que las inferiores. En este caso, esto describe un cono negativo o un ángulo de cono más grande. Si la diferencia de diámetro en el extremo pequeño es mayor, sucede justo lo contrario y en el aparato de medición se lee un cono positivo. No obstante, como un instrumento de medición de conos neumático con pieza de revestimiento solo muestra las diferencias de diámetro, no indica el diámetro parcial en los dos puntos. Por lo tanto, aunque este tipo de instrumentos de medición neumática proporciona una información útil sobre el desgaste del cono de medición y permite predecir la capacidad de ajuste de la forma de la conexión, no es posible emitir ninguna declaración sobre la precisión de posicionamiento de los componentes del cono.
Para ello, se utiliza un instrumento de medición neumático con contacto frontal (a veces también denominado diseño de brida), en el que un alojamiento anular para la medición neumática del cono se dimensiona de forma que pueda albergar todo el cono. Dependiendo de la ubicación de la superficie de referencia de la pieza, esta puede referenciarse en el extremo del cono o en una brida (un resalto) contra la superficie superior de la pieza, lo que permite la medición de diámetros a alturas conocidas (además de la desviación de la holgura, como en el caso de la versión con pieza de revestimiento). También es posible añadir un nivel adicional de toberas de medición para comprobar una cilindricidad cóncava o convexa, es decir, dos condiciones adicionales que reducen el área de contacto entre los dos componentes de ajuste (cono interior y exterior).
El tercer tipo de instrumento de medición de conos neumático es una mezcla de los tipos explicados anteriormente. Se trata básicamente de un instrumento de medición neumático con un pieza de revestimiento y un sensor de medición de longitudes referenciado a la superficie de referencia, lo que permite mostrar la profundidad de inmersión del instrumento de medición neumático en la pieza que va a medirse. Así pues, mientras que el ángulo del cono puede leerse en el aparato de evaluación neumático, la pantalla del sensor de medición de longitudes proporciona una indicación de la profundidad de los diámetros individuales. Al medir una pieza de trabajo con un cono interno, si el paso del cono es demasiado grande, el aparato de medición se hundirá más en la pieza. En cambio, si la pendiente es demasiado pequeña, no se sumergirá tanto en la pieza como se espera. Además, si esta profundidad de inmersión se determina con un palpador de medición, este valor puede utilizarse para calcular los diámetros a cualquier profundidad de medición.
Consideración de la superficie
Debido a la alta precisión y resolución de la metrología neumática, esta puede verse afectada por la calidad de la superficie de la pieza, lo que da lugar a complicaciones en la aplicación de la metrología neumática, pues es necesario disponer de una buena superficie para poder utilizarla. En el uso normal, el chorro de aire de las toberas de medición cubre un área de la superficie de la pieza. A su vez, el chorro de aire se refleja en la superficie para crear la contrapresión necesaria para la medición. En una superficie lisa, la diferencia entre la superficie media y los picos de rugosidad que, en el caso de una pieza de trabajo con diámetro interior, equivalen a la holgura mínima, es más bien insignificante. Sin embargo, si la superficie es muy rugosa, la zona o el lugar donde se acumula la contrapresión puede variar considerablemente. Esto puede registrarse en la pantalla del aparato de medición neumático y tener repercusiones en el diámetro que se muestra.
No obstante, si se producen problemas con la interfaz, pueden tomarse medidas especiales para solucionarlos. Mientras la rugosidad de la superficie sea inferior a Rz 6,3 µm, por lo general, es posible ignorar el desplazamiento. Pero incluso si no es así, cualquier error detectado puede compensarse durante el desarrollo del proceso para, a continuación, mostrar el diámetro real al operario de la máquina. Debido a la naturaleza de las propiedades de la superficie y su reacción cuando la tobera de medición sopla libremente, los amplificadores electrónicos y los PC de medición también pueden proporcionar cálculos fiables de los diámetros medios o máximos.
Conclusión
Los componentes ortopédicos de precisión deben cumplir de forma fiable unos requisitos de calidad extremadamente estrictos. Una de las características dimensionales esenciales que se miden durante el proceso de producción es la estrecha tolerancia de las superficies cónicas para el ajuste de piezas individuales. Como las tolerancias son cada vez más ajustadas, los aparatos de medición también deben ser cada vez más robustos y tener las características de diseño adecuadas para garantizar la correcta sujeción de las piezas. Además, también deben tener la resolución y la precisión adecuadas para medir las tolerancias que se necesitan. Por eso, la metrología neumática se ha convertido ya en el instrumento de verificación preferido a la hora de comprobar estos parámetros tan decisivos.
Traducción del artículo redactado por George Schuetz, director de aparatos de medición de precisión en Mahr Inc.