CNC measuring station for crankshafts and camshafts
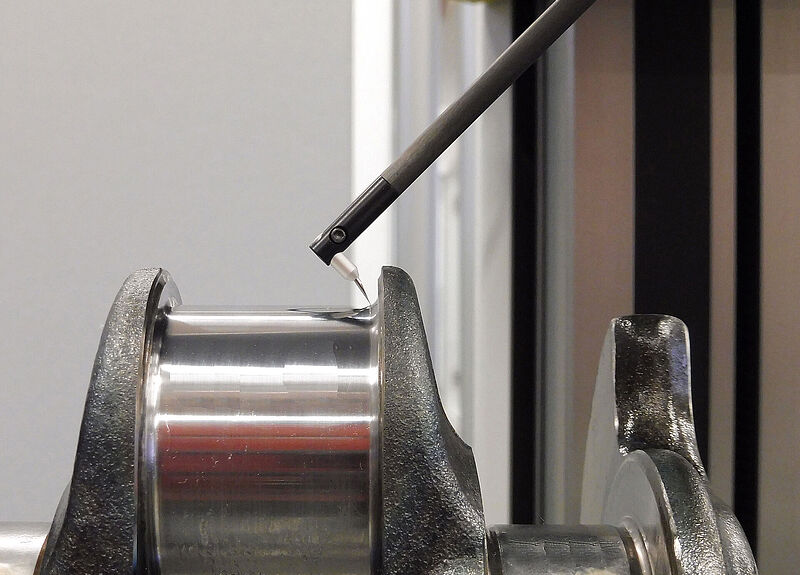
The demand for contour and surface roughness measuring stations continues to grow – as does the desire of many users to automate their measuring processes. Mahr offers a wide range of configuration options for expanding a standard surface measuring station into a high-performance CNC measuring station by adding just a few components. "On the one hand, this is possible through axes and hardware components, and on the other hand, programming is easy to carry out with the MarWin-based standard software via the measurement wizard," explains Karl-Heinz Gödecke, application engineer at the Göttingen-based metrology specialist. "Many applications can be carried out using CNC measuring stations configured in this way, in particular measurements on several workpieces in pallet holders or measurements on the workpiece without reclamping." Additional requirements0- for example, a higher degree of automation, probe arm change comfort, individual axis extension – are solved by the CNC measuring machine line with the MarSurf Xp software.
Contour measurement at the end of the bearing
It is thus possible to measure the roughness parameters, waviness, and material ratios, as well as the radii, distances, angles, straightness, parallelism, and crowning with just one measurement on the CNC measuring station. The measuring station automatically determines and compensates for any radial clamping errors and X-position errors. The measurements of the main and pin bearings are then executed automatically. The CNC axes automatically move to all of the measuring positions in the relevant clamping. This reduces the time required by operators by up to 95 percent compared to a manual measuring station.
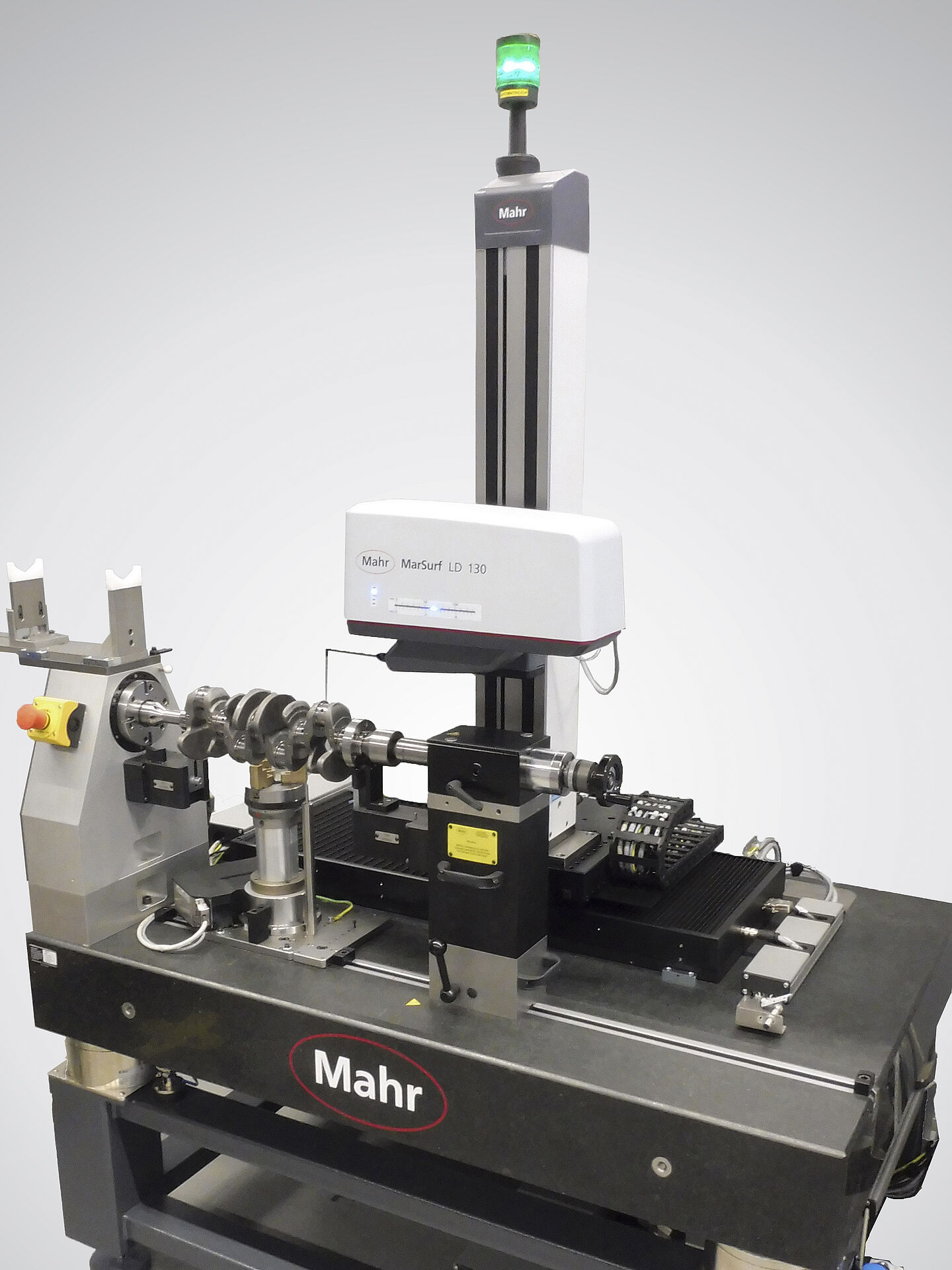
The LD 130 drive unit integrated into the CNC measuring station can be tilted by 45 degrees using the rotational axis of the measuring stand to optimally measure the transition of the bearing in the edge and flange area. The collision protection system installed in and on the LD 130 drive unit, together with the magnetically positioned probe arm and its electrical contact points, ensure reliable protection against collisions.
The roughness and contour in the crankshaft hole are measured in the prisms within the horizontal clamping. In the vertical clamping position, on the other hand, the roughness parameters, distances, and radii of the crankshaft flanges can be determined.
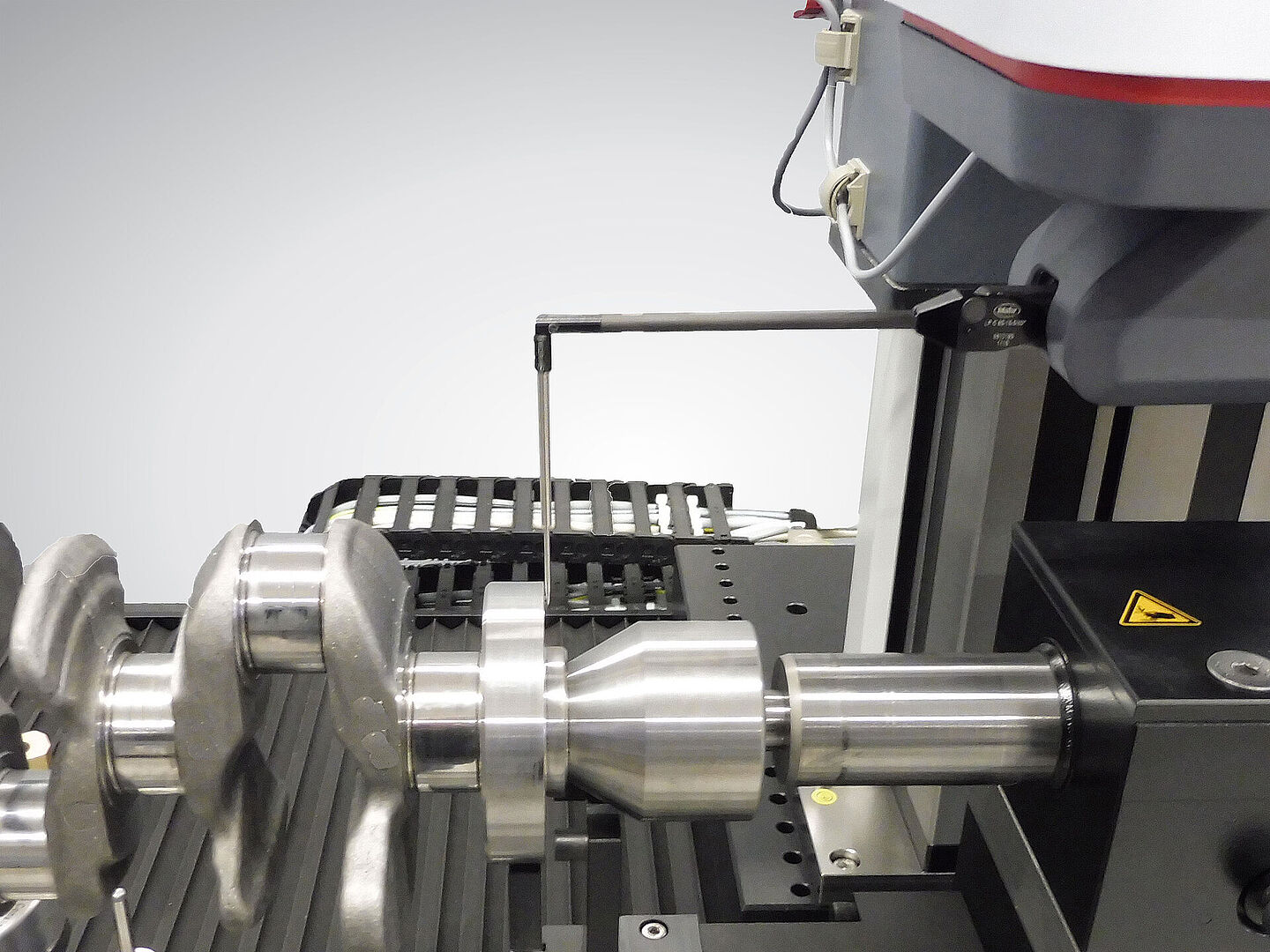
Measuring after brief training with the "CNCplus" program
After just a short training period, operators are able to inspect workpieces quickly and reliably. They are supported by the CNCplus program with specific instructions and images relating to the measuring process. The corresponding inspection plan can be called up automatically based on the workpiece data. "The data is either selected from lists or generated by reading in the DMC code. This ensures that the assigned inspection plan and the correct protocol and export data are loaded automatically," summarizes Gödecke.
The administrator also has the option of selecting the test data, measuring positions, and the characteristics to be tested. This means that measurements can be carried out quickly after setup. Before the measurement is started, the measurement sequence is automatically optimized so that a minimum of inspection cycles are used. The CNCplus program is configured according to the relevant production processes and connections in the production sequences, so that both the menu structure reflects the customer-specific production sequence and the data export is adapted to the individual requirements. Users can thus access known production structures and are familiar with the program's menu structure right from the start.
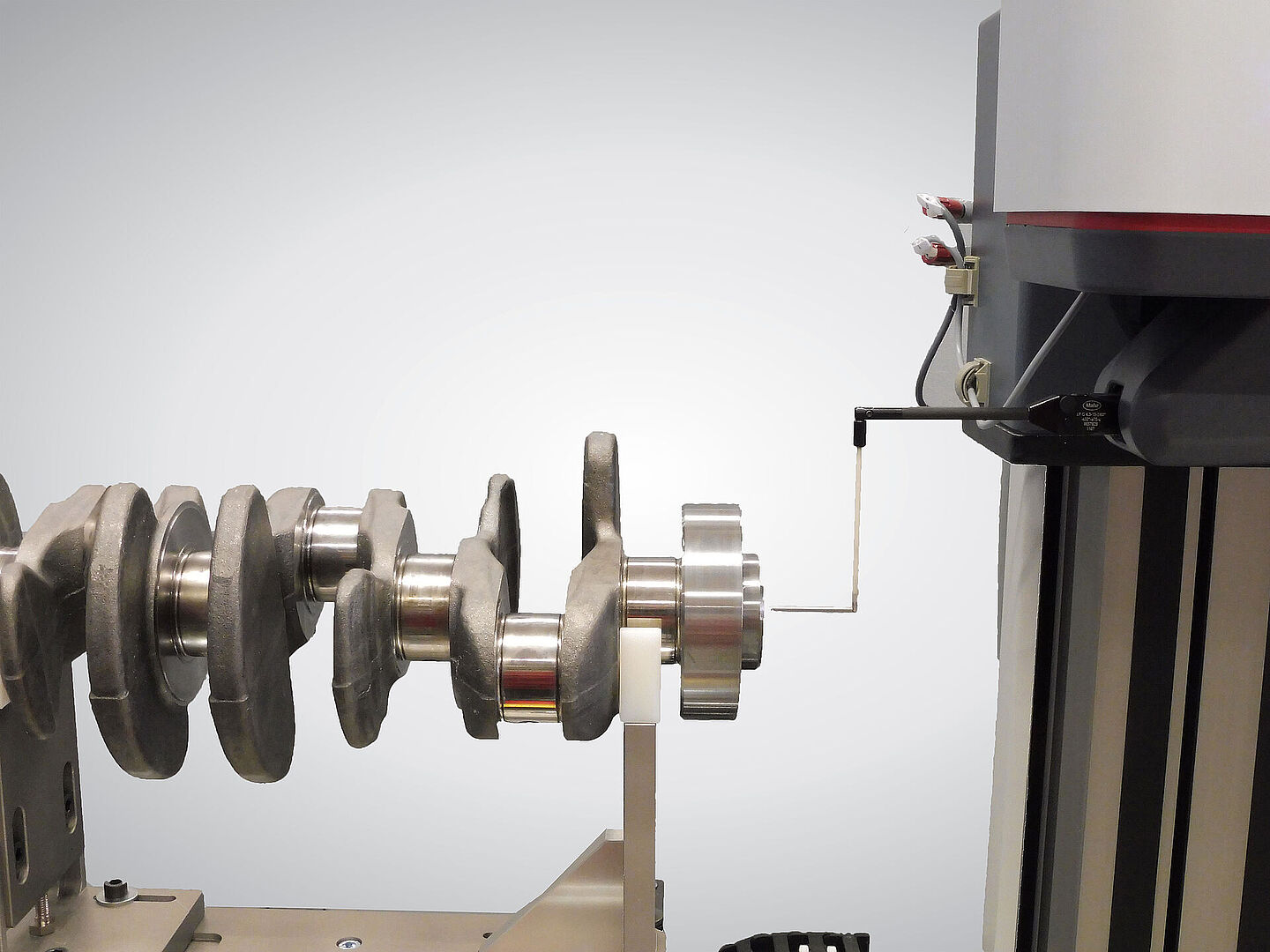
Save time and costs
Thanks to the fully automatic measuring sequences, the operator only has to clamp the crankshaft in the holder and start the program. Compared to a manual measuring station, up to 90 percent less manpower is required to inspect the shaft: The typical inspection time for the bearings and radii of a manually measured 4-cylinder crankshaft with 60 features is around 2.5 hours. In contrast, the same crankshaft can be inspected automatically in 30 minutes using the CNC measuring station, which is 80 percent faster. To measure the crowning of the individual bearing points, the profile is recorded over the entire width of a bearing and the evaluation range is then automatically calculated according to the drawing entry. Finally, the crowning is measured in this area.
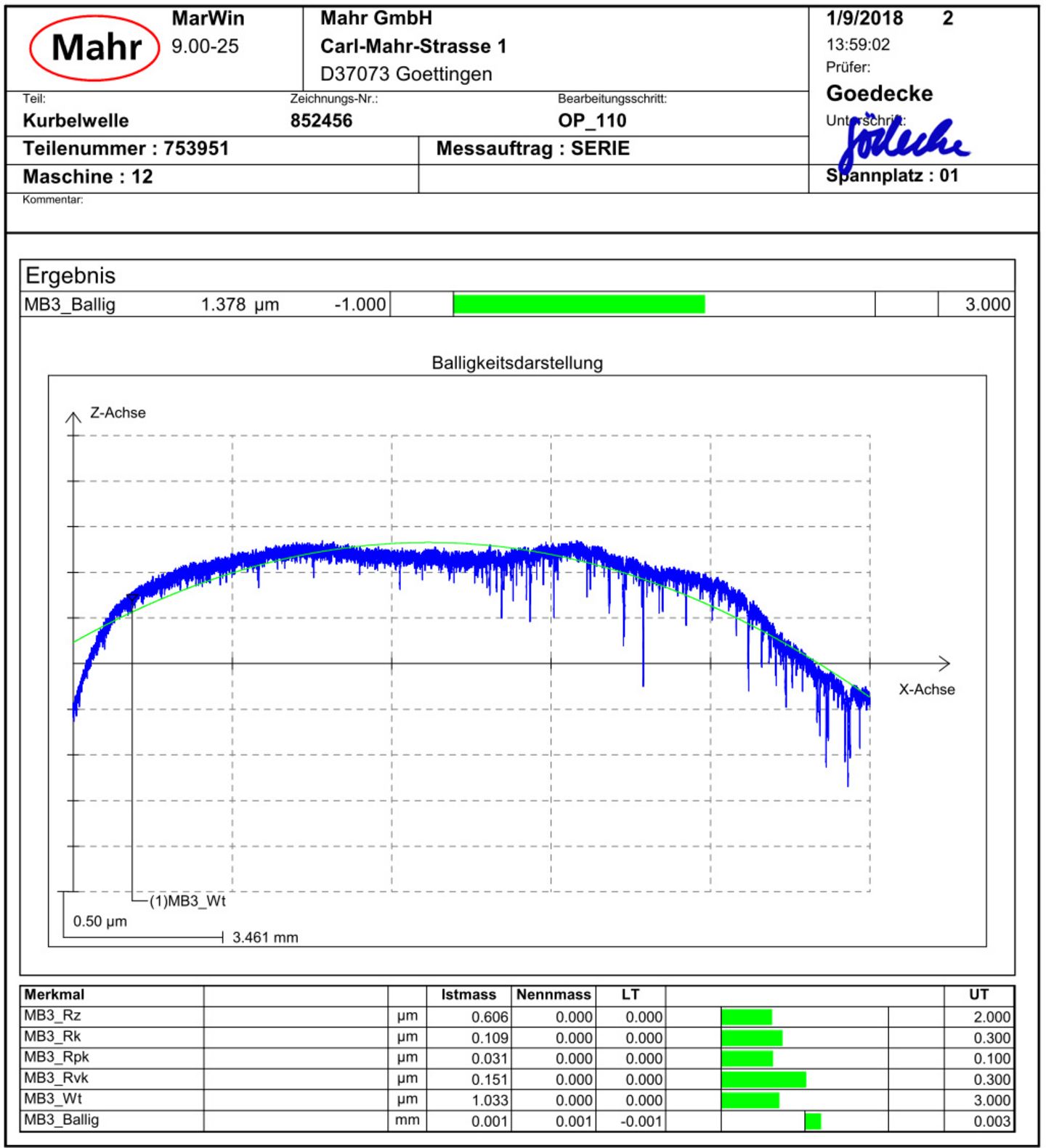
Measuring tasks
- Roughness and core roughness
- Material content
- Waviness
- Straightness
- Crowning
- Distances, radius, angle, position
- Line form deviation
- Tolerance and sum tolerance check