Analyzing surfaces: Is 3D better?
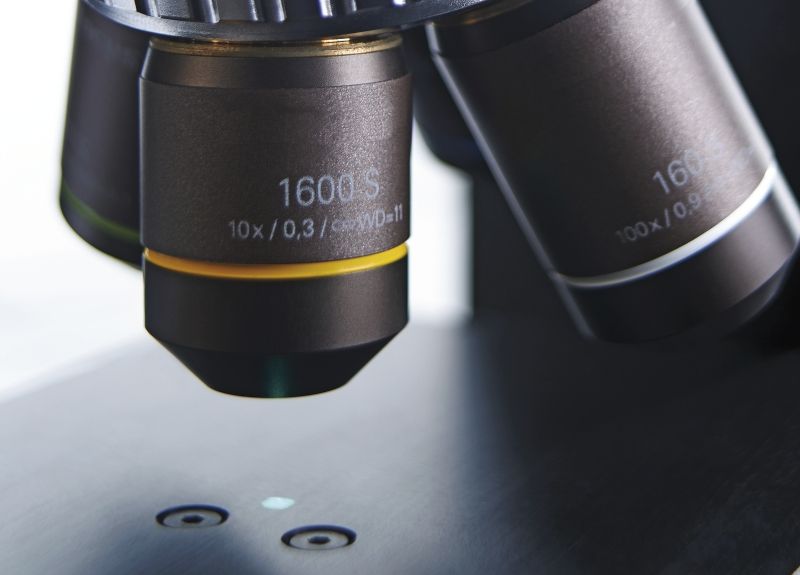
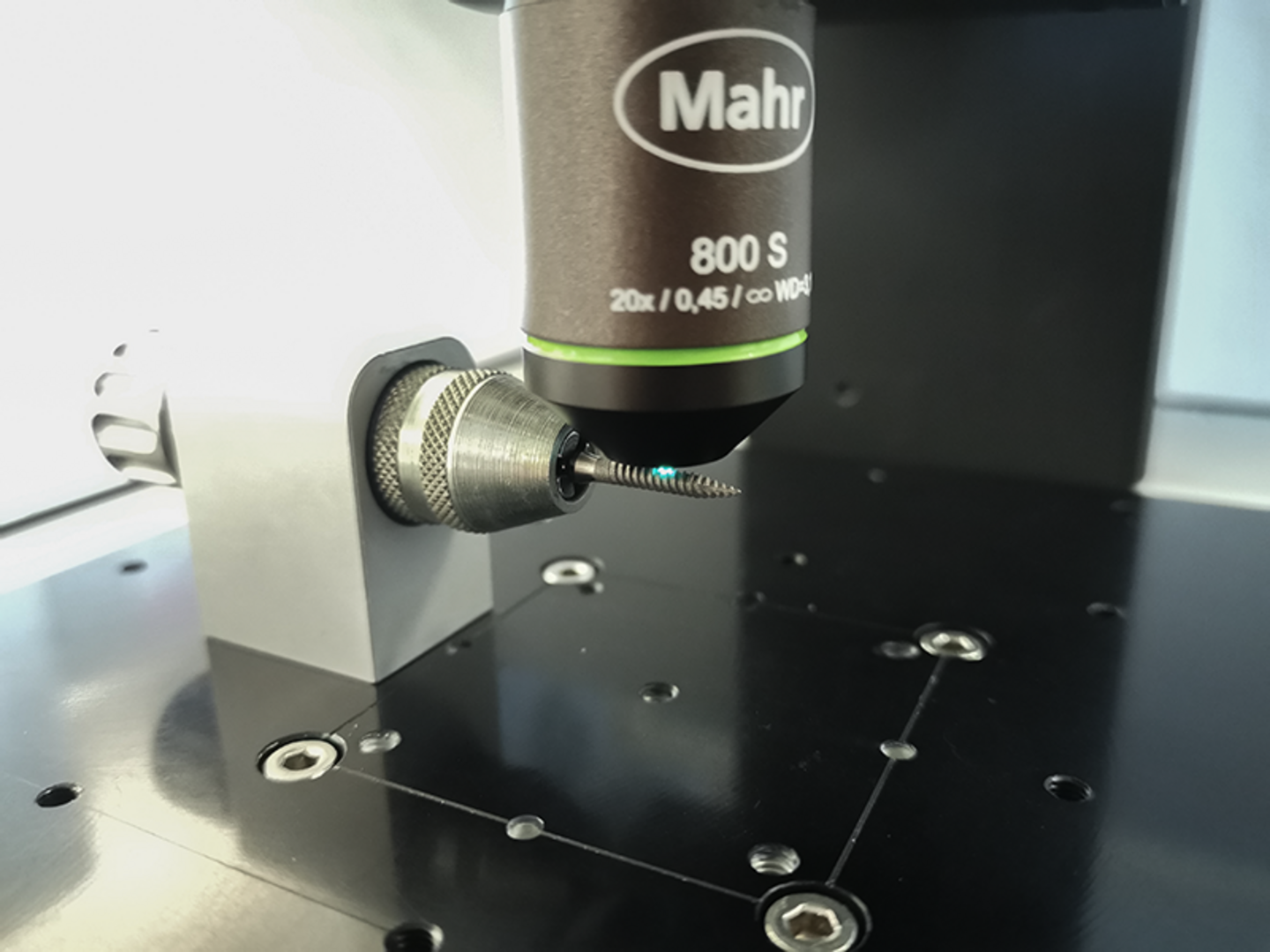
Rauheits- und Welligkeitsmessungen sind etablierte Verfahren in der Qualitätskontrolle. Vermutlich denken auch Sie dabei zunächst an eine taktile, zweidimensionale Messung – wie viele andere Messtechniker übrigens auch. Die so gewonnenen Daten werden dann beispielsweise nach DIN EN ISO 4287 / 4288 oder DIN EN ISO 13565-1/2 ausgewertet. Doch kennen Sie auch die Alternative?
Immer häufiger kommen inzwischen Messsysteme zur optischen, dreidimensionalen Abtastung bei der Oberflächenanalyse zum Einsatz. Mit Ihnen ist eine flächenhafte Analyse der Oberfläche möglich – und zwar auf Basis der DIN EN ISO 25178. Eine solche flächenhafte Bewertung liefert Kennwerte, die sich mittels Tastschnittverfahren nicht (oder nur mit erheblichem Zeitaufwand) ermitteln lassen. Je nach Anwendung ist eine Auswertung der Flächenrauheit also Ihre einzige Chance zu erkennen, ob Ihr Produkt überhaupt die Anforderungen erfüllt.
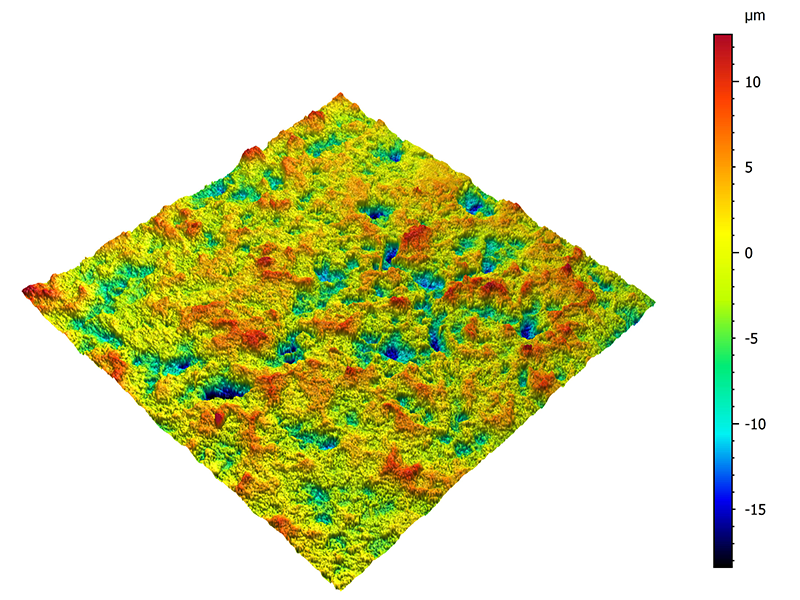
Beispiel Dental-Implantate
Der Einsatz von Implantaten in der Kiefer-Chirurgie erfordert extrem raue und komplexe Oberflächen, an denen die Knochen haften und wachsen können. Eine taktile Abtastung der Implantate ist schon allein aufgrund von Bauform und Werkstückgeometrie schwierig.
Die DIN EN ISO 25178 liefert für dieses Beispiel verschiedene Parameter (Sa, S10z, Sk, Spk und Svk), die statistische Aussagekraft über die flächenhafte Rauheit der Implantate haben. Ähnlich wie die aus der Profilmessung bekannten Pendants (Ra, Rz, Rk, Rpk und Rvk) definieren sie z.B. die mittlere Rauheit oder die Verteilung der Traganteile über die Oberfläche.
Mit der Flächenrauheit zum qualifizierten Ergebnis
Doch welchen Mehrwert bietet 3D? Zusätzlich ermöglichen die Werte nach DIN EN ISO 25178 eine Aussage darüber, wie Erhöhungen, Plateaus und Täler statistisch auf der Fläche verteilt sind. Diese Information ist für den Hersteller zwingend erforderlich, um zu erkennen, ob die Implantate den Anforderungen entsprechen. Gleichzeitig soll die Oberfläche der Implantate möglichst isotrop sein – also keine Vorzugsrichtung aufweisen. Extra hierfür bietet die DIN EN ISO 25178 den Kennwert Str, welcher beschreibt, ob gewisse Strukturen sich auf der Oberfläche in einer Richtung wiederholen. Eine vergleichbare Aussage ist mit einem einzelnen Profilschnitt nicht möglich.
Das passende Verfahren auswählen
Damit steht nun die Frage im Raum, welches Mess- und Auswerteverfahren für Ihren Einsatz am besten geeignet ist. Optisch oder taktil? Profil oder Fläche? Die Entscheidung ist nicht einfach, da sich oftmals sowohl taktile als auch optische Systeme einsetzen lassen – und diese durchaus vergleichbare Daten liefern können. Ohne Anwendungen und Anforderungen im Detail zu kennen, lassen sich jedoch die folgenden Empfehlungen aussprechen:
- Nutzen Sieoptische (also berührungslose) Messverfahren, wenn die zu messende Oberfläche sehr empfindlich oder zu weich, klebrig oder diskontinuierlich ist. Außerdem lassen sich beschichtete und inhomogene Oberflächen oder Oberflächen ohne Bearbeitungsstrukturen besser optisch erfassen.
- Setzen Sie auf dreidimensionale, flächenhafte Messdaten, wenn Sie dabei sind Prozesse zu entwickeln, zu vergleichen oder zu optimieren – oder wenn für Ihren Einsatz noch gar keine Spezifikationen vorhanden sind. Auch wenn Aussehen und Eigenschaften von technischen Oberflächen für die Prozesskontrolle und Fertigungssteuerung untersucht werden, sind 3D-Flächeninformationen von Vorteil.
Das Beispiel der Dental-Implantate zeigt, dass es Anwendungsfälle gibt, in denen eine flächenhafte Analyse erforderlich ist, um eine qualifizierte Aussage zu erhalten. Doch auch wenn nicht zwingend benötigt, ist optische 3D-Messtechnik in vielen Fällen eine gute Alternative zu taktilen Verfahren. Sie bietet Qualitätsprüfern und Prozessentwicklern eine höhere Aussagekraft und somit mehr Sicherheit.