크랭크샤프트 및 캠샤프트용 CNC 측정 스테이션
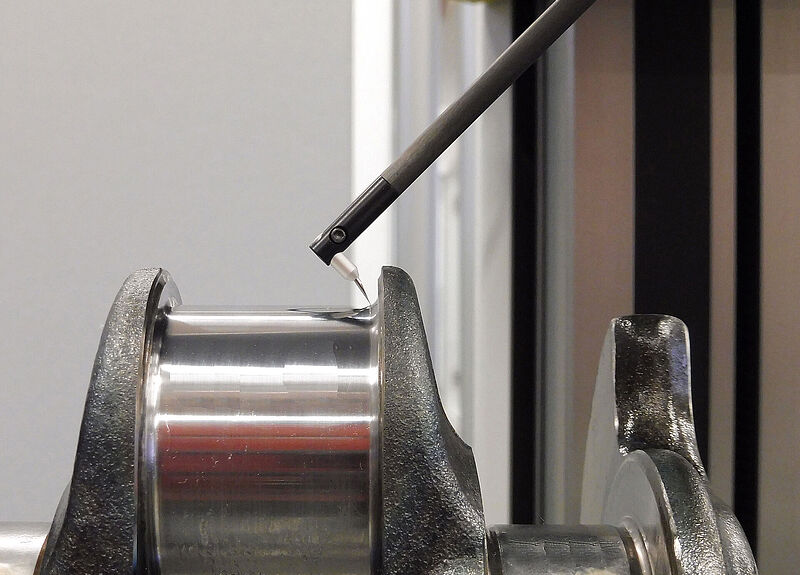
Der Bedarf an Konturen und Rautiefenmessplätzen steigt weiter an – ebenso wie der Wunsch vieler Anwender, die Messabläufe zu automatisieren. Mahr bietet vielfältige Konfigurationsmöglichkeiten, wie sich bereits durch Addition weniger Komponenten ein Standard-Oberflächenmessplatz zu einem leistungsstarken CNC-Messplatz erweitern lässt. „Dies ist zum einen durch Achsen und Hardwarekomponenten möglich, zum anderen ist die Programmierung mit der MarWin-basierten Standard-Software über den Messassistenten einfach durchführbar“, erklärt Karl-Heinz Gödecke, Anwendungsingenieur beim Göttinger Messtechnikspezialisten. „Viele Applikationen lassen sich durch solch konfigurierte CNC-Messplätze ausführen, insbesondere Messungen an mehreren Werkstücken in Palettenaufnahmen oder Messungen am Werkstück ohne Umspannen.“ Darüber hinaus gehende Anforderungen –zum Beispiel ein höherer Automatisierungsgrad, Tastarmwechselkomfort, individuelle Achsenerweiterung – werden durch die CNC-Messmaschinenlinie mit der Software MarSurf Xp gelöst.
Konturenmessung am Lagerende
So ist es beispielsweise mit nur einer Messung am CNC-Messplatz möglich, sowohl Rauheitskennwerte, Welligkeit und Materialanteile als auch Radien, Abstände, Winkel, Geradheit, Parallelität und Balligkeit zu messen. Der Messplatz ermittelt automatisch radiale Aufspannfehler und X-Positionsfehler und kompensiert diese. Anschließend werden die Messungen der Haupt- und Hublager vollautomatisch durchgeführt. Die CNC-Achsen fahren alle Messorte in der jeweiligen Aufspannung von selbst an. Dadurch reduziert sich der Zeitaufwand für Bediener um bis zu 95 Prozent gegenüber einem manuellen Messplatz.
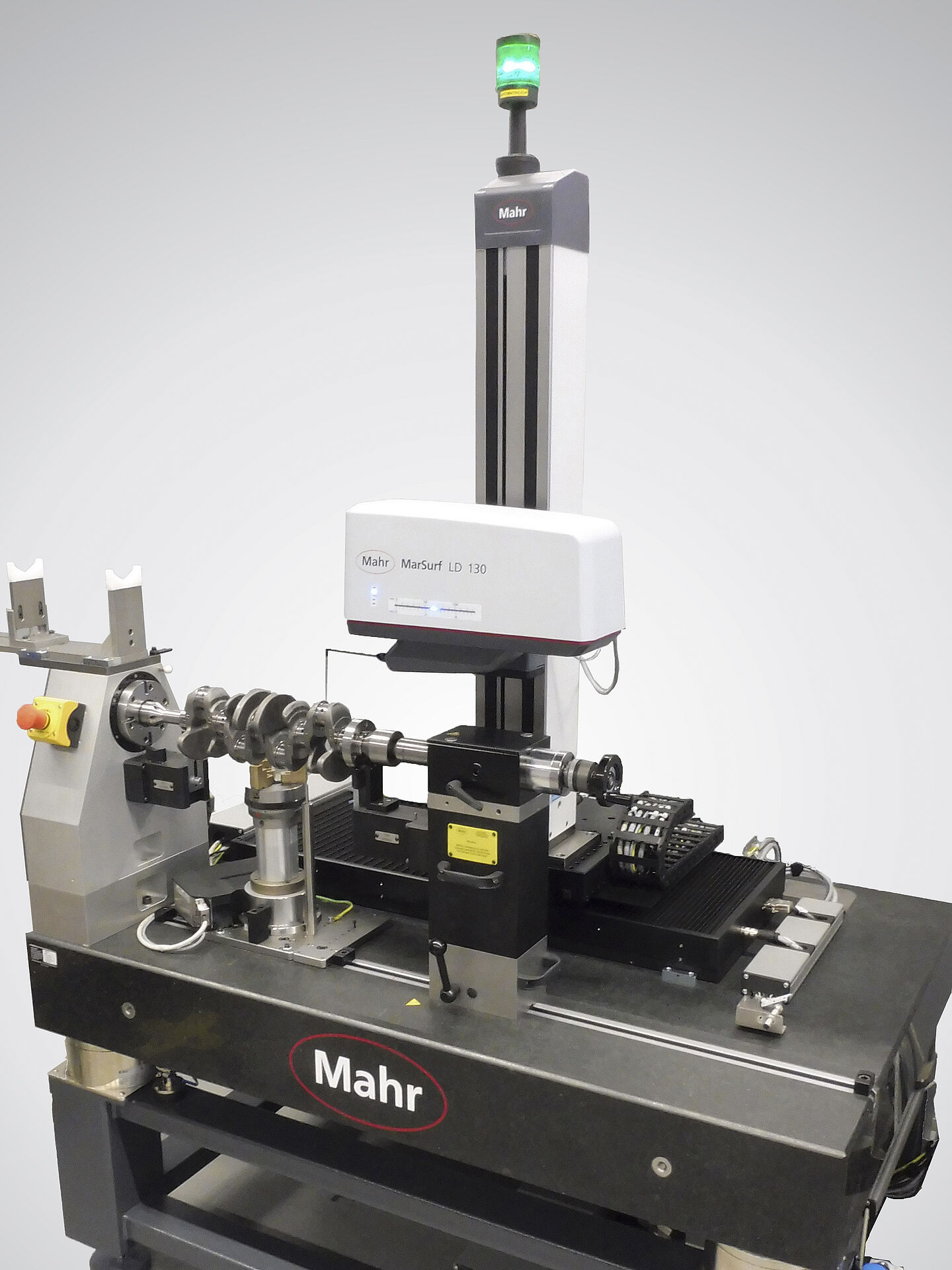
Das in den CNC-Messplatz integrierte Vorschubgerät LD 130 lässt sich mit der Rotationsache des Messständers um 45 Grad neigen, um den Übergang des Lagers im Rand- und Wangenbereich optimal zu messen. Das im und am Vorschubgerät LD 130 installierte Kollisionsschutzsystem sorgt zusammen mit dem magnetisch gehaltenen Tastarm und seinen elektrischen Kontaktpunkten für einen zuverlässigen Schutz gegen Kollisionen.
In der horizontalen Aufspannung in Prismen werden die Rauheit und die Kontur in der Kurbelwellenbohrung gemessen. In der vertikalen Spannlage lassen sich hingegen die Rauheitskennwerte, Abstände und Radien der Kurbelwellenwangen.
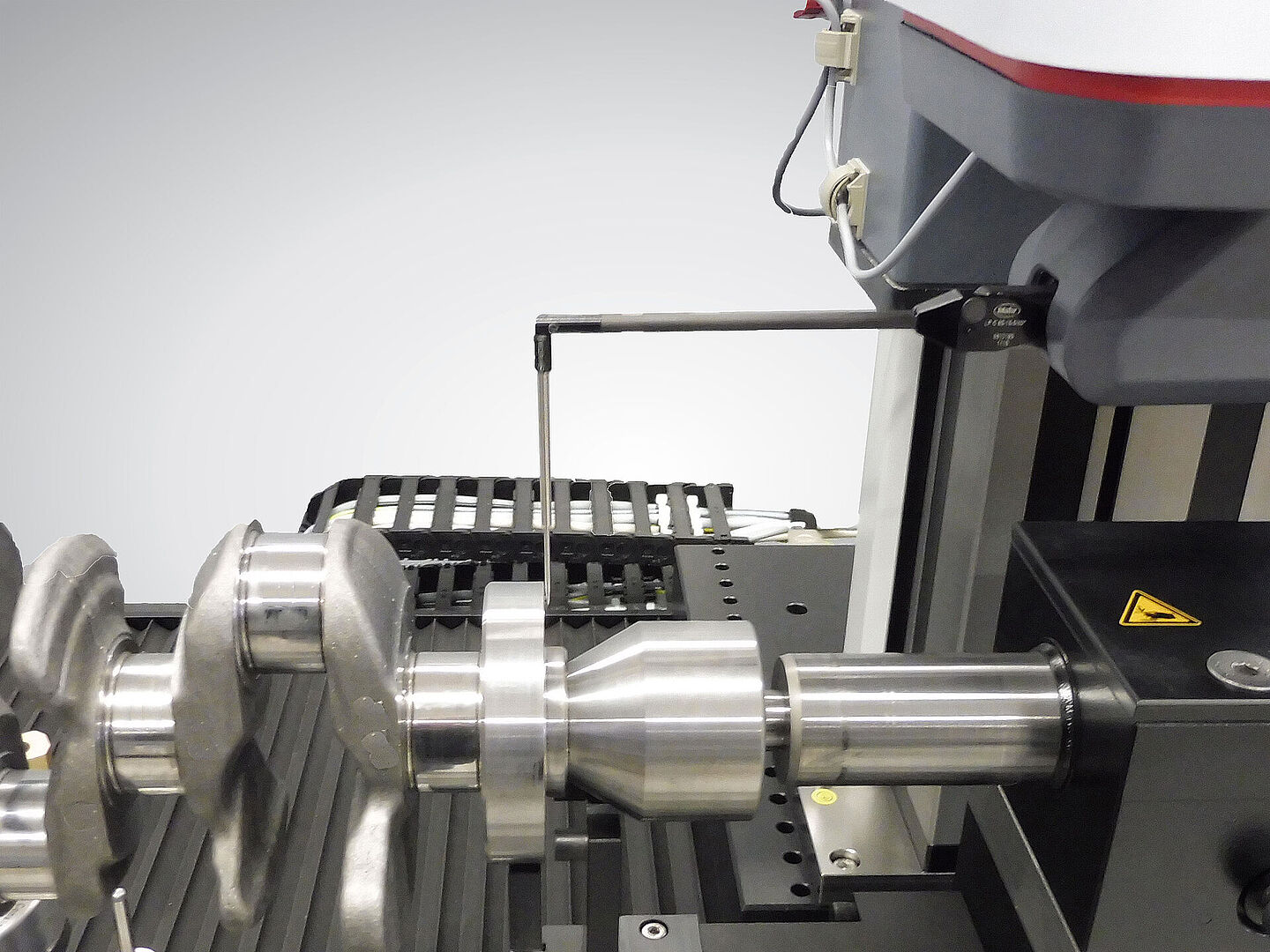
Messen nach kurzer Einweisung mit dem Programm „CNCplus“
Bereits nach einer kurzen Einarbeitung sind Bediener in der Lage, die Werkstücke schnell und zuverlässig zu prüfen. Dabei werden sie vom Programm CNCplus mit konkreten Hinweisen und Bildern bezüglich des Messablaufs unterstützt. Anhand der Werkstückdaten lässt sich der entsprechende Prüfplan automatisch aufrufen. „Die Daten werden entweder aus Listen ausgewählt oder durch das Einlesen des DMC-Codes generiert. Dadurch ist sichergestellt, dass automatisch der zugeordnete Prüfplan und die richtigen Protokoll- und Exportdaten geladen werden“, fasst Gödecke zusammen.
Der Administrator hat zudem die Möglichkeit, die Prüfdaten, Messorte sowie die zu prüfenden Merkmale auszuwählen. Somit lassen sich Messungen zügig nach dem Einrichten schnell ausführen. Vor dem Starten der Messung wird der Messablauf automatisch optimiert, sodass daraus minimale Prüfzyklen resultieren.
Entsprechend der jeweiligen Fertigungsprozesse und Abhängigkeiten in den Produktionsabläufen wird das CNCplus-Programm konfiguriert, sodass sowohl die Menüstruktur den kundenspezifischen Fertigungsablauf widerspiegelt als auch der Datenexport gemäß den individuellen Anforderungen angepasst wird. Anwender finden also bekannte Fertigungsstrukturen vor und sind von Beginn an mit der Menüstruktur des Programms vertraut.
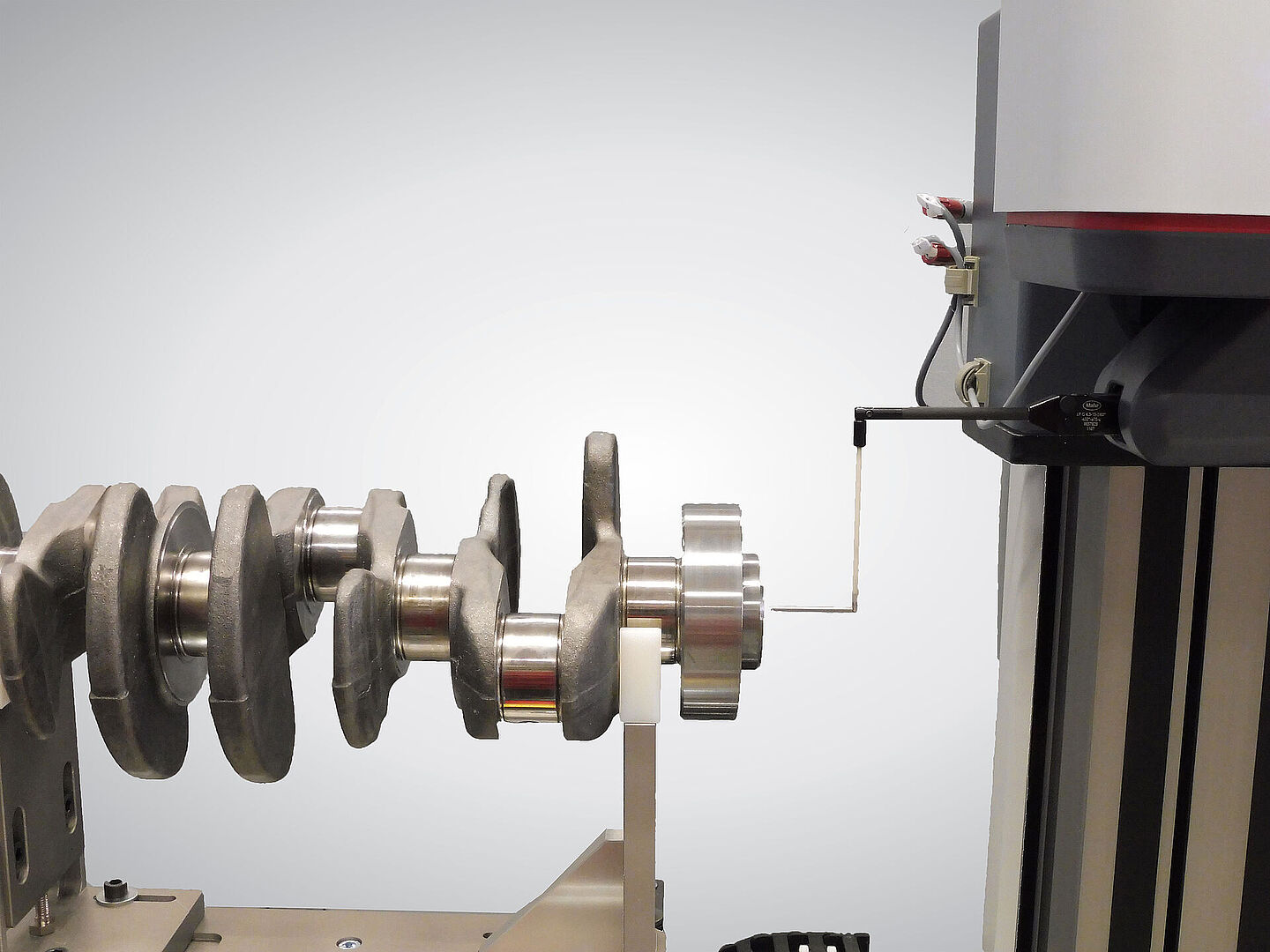
Zeit und Kosten sparen
Aufgrund der vollautomatischen Messabläufe muss der Bediener die Kurbelwelle nur in die Aufnahme spannen und das Programm starten. Gegenüber einem manuellen Messplatz lassen sich bis zu 90 Prozent Personalaufwand für die Prüfung der Welle einsparen: Die typische Prüfzeit der Lager und Radien einer manuell gemessenen 4-Zylinder-Kurbelwelle mit 60 Merkmalen beträgt rund 2,5 Stunden. Demgegenüber wird dieselbe Kurbelwelle mit dem CNC-Messplatz in 30 Minuten automatisch durchgeführt und ist somit 80 Prozent schneller.
Für die Messung der Balligkeit der einzelnen Lagerstellen wird das Profil über der gesamten Breite eines Lagers aufgezeichnet und anschließend der Auswertebereich entsprechend der Zeichnungseintragung automatisch berechnet. Schließlich wird die Balligkeit in diesem Bereich gemessen.
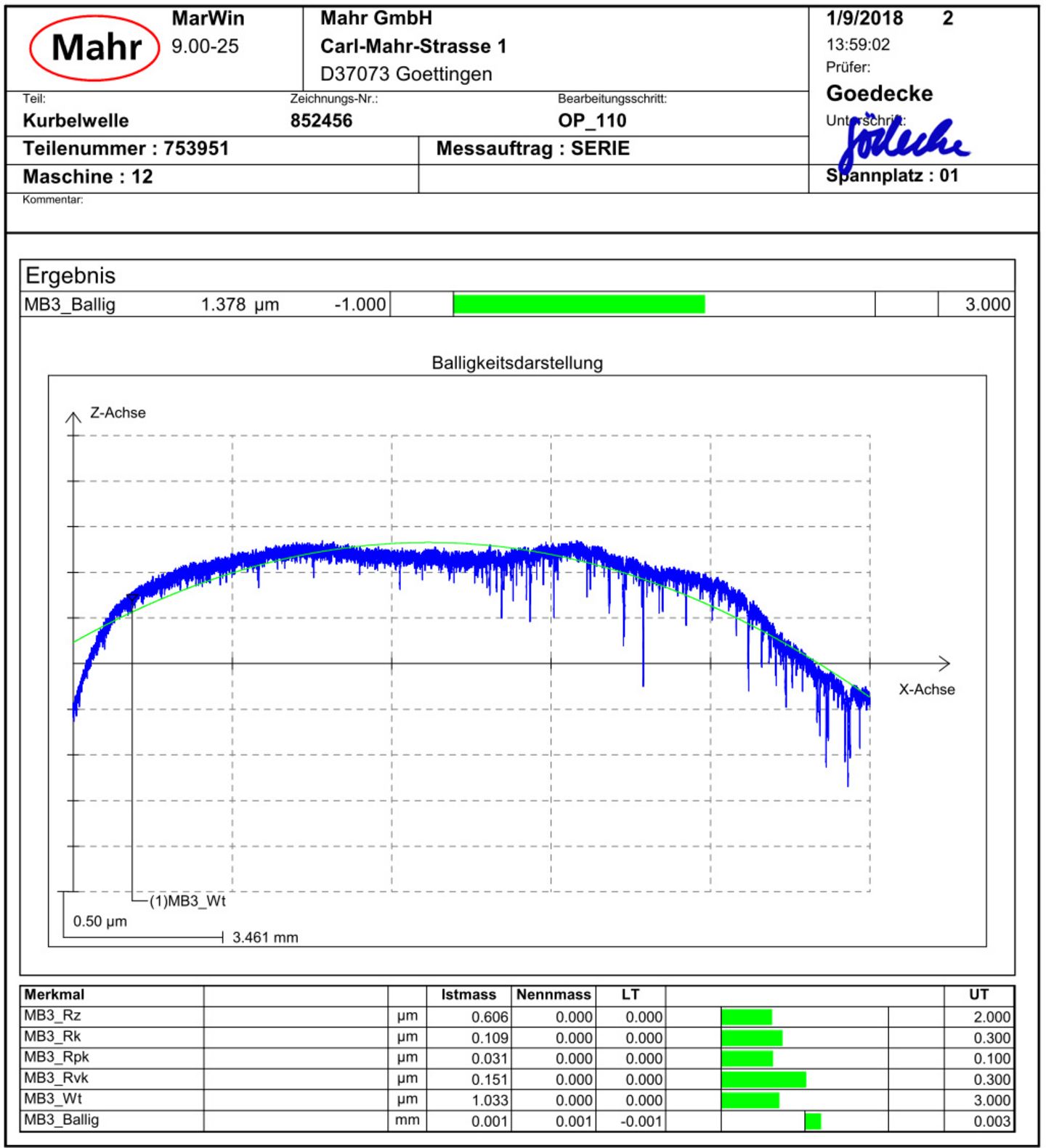
Messaufgaben
• Rauheit und Kernrauheit
• Materialanteil
• Welligkeit
• Geradheit
• Balligkeit
• Abstände, Radius, Winkel, Position
• Linienformabweichung
• Toleranz- und Summentoleranzüberprüfung