Using Air Gaging for Measurement of Orthopedic Devices
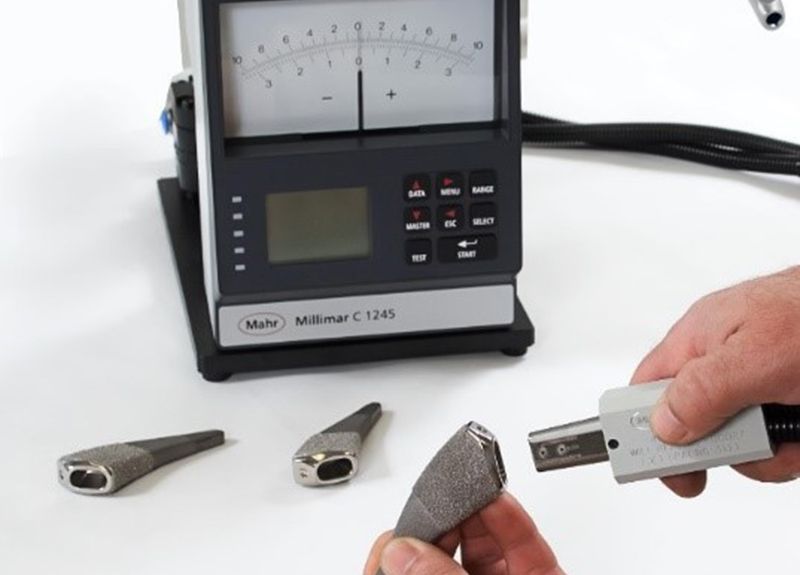
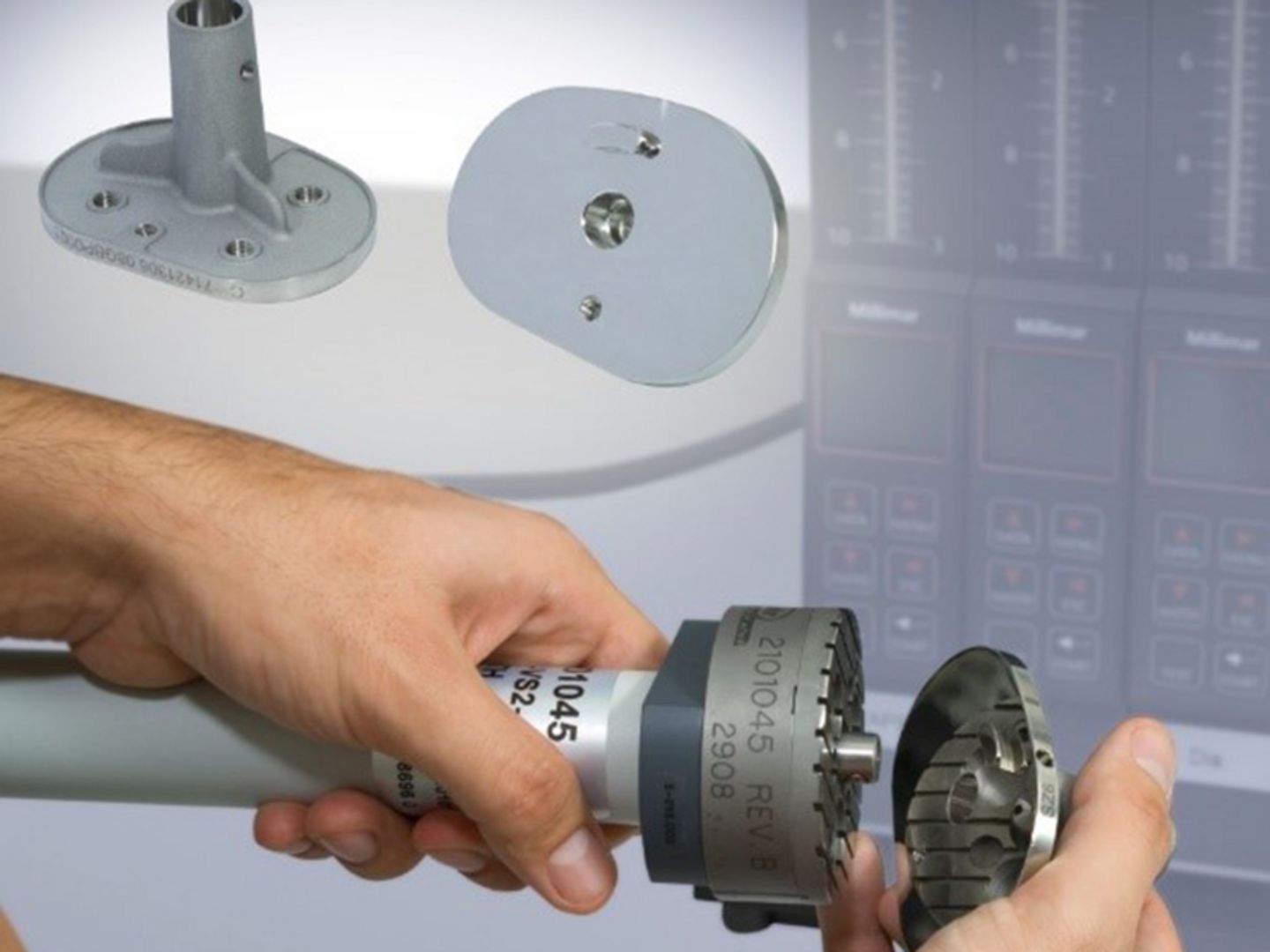
Orthopädische Präzisionskomponenten können nur dann die hohen Qualitätsstandards erfüllen, wenn jeder einzelne Fertigungsschritt (vom ersten Zuschnitt bis hin zur Endbearbeitung) konsequent stabil ist. Dies erfordert eine prozessorientierte Überprüfung der Merkmale, ein umgehendes Feedback bei Toleranzüberschreitungen und das Dokumentieren aller Prozessdaten.
Typischerweise werden, während die Werkstücke vom Rohmaterial bis hin zum Endprodukt den Fertigungsprozess durchlaufen, Maßtoleranz, Oberflächengüte und geometrische Merkmale zunehmend kritischer – umso kritischer ist es, diese Toleranzen einzuhalten bzw. zu erkennen, wann sie überschritten sind. Eines der Maßmerkmale, die am Ende des Fertigungsprozesses orthopädischer Vorrichtungen gemessen werden, ist die enge Toleranz an den Kegelflächen zur Passung der einzelnen Teile. Beispielsweise verwenden die meisten Hüft- und Knieimplantate Kegelflächen zur optimalen Ausrichtung und sicheren „Arretierung“ der Komponenten in der richtigen Position. Schon bei der Herstellung dieser Teile entscheidet die Kontrolle der Kegelform und Größe darüber, wie gut die Leistung der orthopädischen Implantate während deren Lebensdauer sein wird.
Warum ist die pneumatische Messtechnik die wirksamste Methode?
Angesichts der zunehmend engeren Toleranzen müssen die Messgeräte immer robuster sein und die richtigen Auslegungsmerkmale besitzen, damit die Teile korrekt aufgespannt werden. Sie müssen außerdem die zur Messung der geforderten Toleranzen geeignete Auflösung und Genauigkeit aufweisen. Die pneumatische Messtechnik hat sich hier mehr und mehr zum bevorzugten Prüfinstrument für die Kontrolle dieser kritischen Parameter entwickelt. Pneumatische Messgeräte sind außerordentlich präzise und bieten sehr hohe Auflösungen. Sie werden typischerweise für Anwendungen eingesetzt, bei denen die Toleranzen eng sind — üblicherweise unter ± 25 µm — und die Oberflächenrauheit weniger als Rz 6,3 µm beträgt. Wenn diese Bedingungen vorliegen, wie beispielsweise bei Präzisionskegeln für medizinische Anwendungen, stellt die pneumatische Messtechnik oft die beste Lösung dar.
Besonders gut eignet sich das pneumatische Messen auch zur Prüfung von Maßverhältnissen; pneumatische Messgeräte sind schnell, einfach zu bedienen und weisen selbst unter härtesten Einsatzbedingungen in der Fertigung eine Lebensdauer von vielen Jahren auf — um Millionen von Teilen messen zu können. In einigen Fällen kann die pneumatische Messtechnik sogar zur Prüfung und Beurteilung bestimmter Formmerkmale eines Teils eingesetzt werden.
Die Messdüse, also jene kleine Öffnung aus der die Luft ausgegeben wird, ist der Grund dafür, dass die Pneumatische Messtechnik so nützlich zur Messung orthopädischer Kegelflächen ist. Kein anderer Messsensor ist so klein oder kann so nah an der Messstelle angeordnet werden, wenn es mehrere Durchmesser oder geometrische Formen zu messen gilt. Kleine elektronische Sensoren oder Wirbelstromsensoren können sich zwar der Größe einer Messdüse annähern, aber nicht mit ihrer Wirtschaftlichkeit oder Eignung zum direkten Einsatz bei der Produktion im Fertigungsbereich mithalten.
Es ist möglich, Durchmesser und Kegel entweder mittels einer Kombination elektronischer Sensoren oder aber per Koordinaten-Messgerät (KMG) mit Kantentastern zu messen. Die Messdüse kann direkt in ein Präzisionsgerät eingebaut werden, sodass sie zur Messung des Teils direkt in der Fertigung einsetzbar ist. So kann die Messung in einem schnellen Messvorgang mit minimalem Bedieneraufwand erledigt werden. Weder KMG noch optische Messtechnik bieten hier die erforderliche Schnelligkeit und Genauigkeit, um eine 100 prozentige Kontrolle der Werkstücke in der Fertigung zu realisieren und ein sofortiges Feedback zur Prozessleistung bereitzustellen.
Auswahl der richtigen Prüfmittelauslegung
Es gibt praktisch ebenso viele Methoden zur Festlegung von Kegelanforderungen wie Hersteller von Kegelkomponenten. Die Bezugsfläche kann von Hersteller zu Hersteller variieren und die Toleranzen können auf verschiedene Weise angegeben werden.
Je nachdem, wie die Teile zu einer Einheit zusammengefügt werden, können die Toleranzen am Kegel enger sein als an den Durchmessern oder umgekehrt. Alternativ kann auch eine Kombination von Kegeltoleranzen an nur einem Durchmesser vorgegeben sein. Somit ist die Angabe auf der Zeichnung die beste Leitlinie bei der Auswahl der geeignetsten Ausführung des pneumatischen Messmittels. Bei der pneumatischen Messtechnik sind die Prüfmittel jeweils speziell für jede verschiedene Kegelanwendung angefertigt, so dass es entscheidend ist, die Anforderungen werkstückspezifisch zu betrachten. Dennoch sind die Flexibilität und die Vorzüge dieser Messmethode nahezu unschlagbar: sie bietet sehr hohe Auflösungen und die Messsensoren können vielfach kombiniert werden, um direkt in der Fertigung jede beliebige Anzahl von dimensionellen und geometrischen Messdaten zu erhalten.
Verschiedene Arten pneumatischer Kegelmessmittel
Medizinische Implantate müssen außerordentlich haltbar und widerstandsfähig sein, so dass die Kegelpassung zwischen Matrize und Patrize sehr genau sein muss. Die beiden Teile müssen sicher miteinander verbunden sein und auf der korrekten Höhe sitzen. Bei der Herstellung ist es übliche Praxis, 100 Prozent der Teile zu prüfen, um die Fertigungsgenauigkeit beider Komponenten sicherzustellen. Dies erfolgt in der Regel mittels der differentialen pneumatischen Messtechnik, welche die notwendige hohe Auflösung und Genauigkeit mit der im Fertigungsbereich geforderten Schnelligkeit, einfachen Bedienung und Robustheit kombiniert.
Der gängigste Typ eines pneumatischen Kegelmessmittels weist zwei Düsenpaare in zwei Messebenen auf und ist für die Mantelanlage zwischen Werkstück und Messmittel ausgelegt (siehe Abbildungen). Ist der Kegelwinkel zu groß, besteht am kleineren Kegelende mehr Spiel zwischen den beiden Oberflächen. Ist der Kegelwinkel zu klein, besteht am größeren Ende mehr Spiel. In beiden Fällen kann dies den Formschluss der Verbindung verringern, wodurch die „sichere Verbindung“ im Laufe der Zeit verloren gehen kann, indem sie sich lockert bzw. durchdreht. Ist der Kegelwinkel korrekt, aber die Größe falsch, führt dies zu einer falschen Gesamtlänge der orthopädischen Einheit und damit zu unerwarteten Ergebnissen nach der Implantation.
Für Kegeldüsenmessdorne mit Mantelanlage messen keine Teildurchmesser, sondern zeigen vielmehr die Durchmesserdifferenz an zwei Messstellen auf dem Werkstück an, die dann mit den entsprechenden Messstellen des Normals bzw. des Meisters verglichen werden. Falls die Durchmesserdifferenz am großen Ende des Kegels größer ist als die Durchmesserdifferenz am kleinen Ende, werden die oberen Düsen mehr Gegendruck erkennen als die unteren Düsen. Dies beschreibt in diesem Fall einen negativen Kegel bzw. einen größeren Kegelwinkel. Ist die Durchmesserdifferenz am kleinen Ende größer, liegt der umgekehrte Fall vor und am Messgerät ist ein positiver Kegel abzulesen. Da jedoch ein Pneumatisches Kegelmessmittel mit Mantelanlage nur Durchmesserdifferenzen anzeigt, wird es nicht den Teildurchmesser an den beiden Stellen anzeigen. So liefert diese Art pneumatischer Messmittel zwar gute Angaben zum Verschleiß des Messkegels und erlaubt die Vorhersage einer Formschlussfähigkeit der Verbindung, kann jedoch nichts über die Positioniergenauigkeit der Kegelkomponenten aussagen.
Hierzu wird ein Pneumatisches Messmittel mit Stirnanlage (bisweilen auch als Flansch-Ausführung bezeichnet) verwendet, bei dem eine ringförmige Aufnahme zur pneumatischen Kegelmessung so dimensioniert ist, dass sie den gesamten Kegel aufnehmen kann. Je nachdem, wo sich die Bezugsfläche des Teils befindet, kann das Teil auf dem Ende des Kegels oder auf einem Flansch (einer Schulter) gegen die obere Teileoberfläche referenziert werden. Dies ermöglicht die Messung von Durchmessern auf bekannten Höhen (zusätzlich zu der Spielabweichung, wie bei der Ausführung mit Mantelanlage). Eine zusätzliche Ebene an Messdüsen kann ergänzt werden, um eine konkave bzw. konvexe Zylinderform zu prüfen, d. h. zwei weitere Bedingungen, welche die Kontaktfläche zwischen den beiden Passformkomponenten (Innen- und Außenkonus)verringern.
Der dritte Typ pneumatischer Kegelmessmittel ist eine Mischung aus den zuvor erläuterten Arten. Dabei handelt es sich im Wesentlichen um ein Pneumatisches Messmittel mit Mantelanlage und einem Längenmesssensor, der auf die Oberfläche der Bezugsfläche referenziert ist. Somit kann angezeigt werden, wie tief das pneumatische Messmittel in das zu messende Teil eintaucht. Während also am pneumatischen Auswertegerät der Kegelwinkel abzulesen ist, liefert die Anzeige des Längenmesssensors eine Tiefenangabe der Einzeldurchmesser. Beim Messen eines Werkstücks mit Innenkegel wird, wenn die Kegelsteigung zu groß ist, das Messgerät weiter in das Teil eintauchen. Ist die Steigung zu klein, wird es nicht so weit wie erwartet in das Teil eintauchen. Wird diese Eintauchtiefe mit einem Messtaster ermittelt, kann dieser Wert zur Berechnung der Durchmesser in beliebigen Messtiefen herangezogen werden.
Berücksichtigung der Oberfläche
Aufgrund der hohen Genauigkeit und Auflösung der pneumatischen Messtechnik kann diese durch die Oberflächengüte des Teils beeinflusst werden. Dies führt zu Komplikationen bei der Anwendung der pneumatischen Messtechnik, da für deren Einsatz eine gute Oberfläche erforderlich ist. Bei normalen Gebrauch bedeckt der Luftstrahl der Messdüsen einen Bereich der Oberfläche des Teils. Der Luftstrahl wird von der Oberfläche reflektiert, um den für die Messung erforderlichen Gegendruck zu erzeugen. Auf einer glatten Oberfläche ist die Differenz zwischen der durchschnittlichen Oberfläche und den Rauheitsspitzen, die im Falle eines Innendurchmesser-Werkstücks gleichbedeutend mit minimalem Spiel sind, eher unerheblich. Ist jedoch die Oberfläche sehr rau, kann der Bereich bzw. die Stelle, an dem der Gegendruck aufgebaut wird, erheblich abweichen. Dies kann auf der Anzeige des pneumatischen Messgeräts registriert werden und sich auf den angezeigten Durchmesser auswirken.
Allerdings können bei Problemen mit der Oberfläche spezielle Schritte unternommen werden, um diese zu berücksichtigen. So lange die Oberflächenrauheit unter Rz 6,3 µm liegt, kann das Offset normalerweise ignoriert werden. Aber selbst wenn nicht kann ein Fehler, welcher während der Prozessentwicklung entdeckt wird, kompensiert und der tatsächliche Durchmesser dem Maschinenbediener angezeigt werden. Durch die Gegebenheit der Oberflächenbeschaffenheit und deren Reaktion bei frei abblasender Messdüse können elektronische Verstärker und Messrechner auch zuverlässige Berechnungen von mittleren oder maximalen Durchmessern bereitstellen.
Schlussfolgerung
Orthopädische Präzisionskomponenten müssen zuverlässig extrem hohe Qualitätsstandards erfüllen. Eines der kritischen Maßmerkmale, die während des Fertigungsprozesses gemessen werden, ist die enge Toleranz an den Kegelflächen zur Passung der einzelnen Teile. Angesichts der zunehmend engeren Toleranzen müssen die Messgeräte robuster sein und die richtigen Auslegungsmerkmale besitzen, damit die Teile korrekt aufgespannt werden. Außerdem müssen sie die zur Messung der geforderten Toleranzen geeignete Auflösung und Genauigkeit aufweisen. Die pneumatische Messtechnik hat sich mehr und mehr zum Prüfinstrument erster Wahl für die Kontrolle dieser kritischen Parameter entwickelt.
Artikel verfasst von George Schuetz, Director Precision Gages bei Mahr Inc.