Improved standards for surface texture
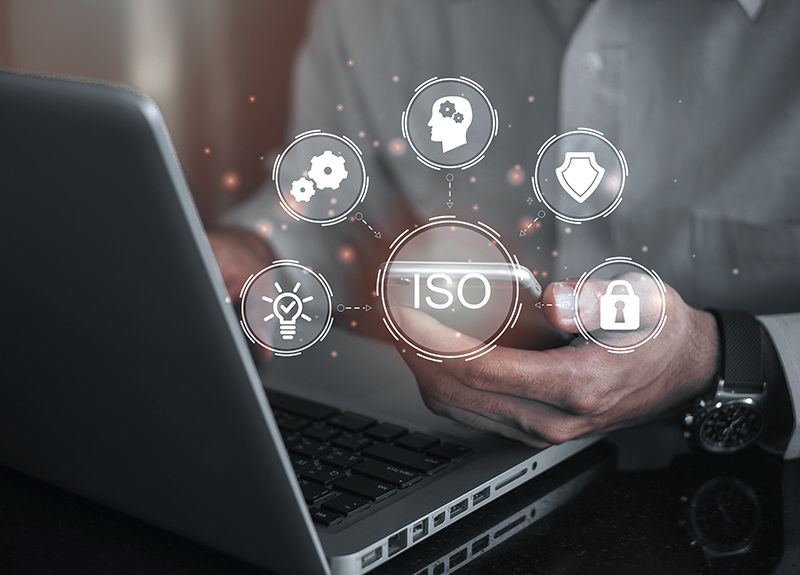
Wer ein Blatt Papier in den Drucker legt, denkt nicht lange darüber nach: Die Papiergröße passt zum Drucker, der Drucker passt zum Papier. Das ist kein Zufall, sondern Ergebnis einer Norm. Laut Deutschem Institut für Normung e. V. (DIN) bilden aktuell rund 34.000 Normen das Deutsche Normenwerk. Sie geben Herstellern und Verbrauchern wichtige Regeln an die Hand, setzen Standards für Produkte und Verfahren und schaffen klare Kriterien – oft sogar weltweit.
Und so sind die drei Teile des neuen Standardwerks ISO 21920 Profilnormen ein wichtiger Baustein in dem seit fast 25 Jahren erarbeiteten internationalen Normenkonzept der Geometrischen Produktspezifikation (GPS-System). Nach den bereits veröffentlichten Normen zur flächenhaften Spezifikation der Oberflächenbeschaffenheit, der Normreihe DIN EN ISO 25178, stehen mit DIN EN ISO 21920 auch die relevanten Profilnormen in aktualisierter Fassung zur Verfügung. Die bisherigen Profilnormen
- ISO 4287:1997-04 „Kenngrößen“
- ISO 4288:1996-08 „Messbedingungen“
- ISO 13565-1 bis 3 „Traganteil“
- ISO 1302:2002-02 „Zeichnungseintragungen“
werden zurückgezogen. „Sie decken nicht mehr alle Möglichkeiten moderner Messgeräte ab – etwa, weil sie bis dato keine standardisierten Verfahren für die optischen Messgeräte boten. Zudem entsprachen sie nicht immer der aktuellen industriellen Praxis und hatten teilweise Unschärfen in der Definition einiger Kennwertalgorithmen“, erklärt Heinz-Joachim Kedziora, Leiter der Entwicklung Oberflächenmesstechnik bei Mahr. Er ist zugleich als Projektleiter für den dritten Teil der neuen Norm international verantwortlich und hat im Sommer 2021 diese Aufgabe auch für den ersten Norm-Teil übernommen. „Die DIN EN ISO 12085 („Motif“) bleibt bestehen; mit der Überarbeitung der DIN EN ISO 3274 („Tastschnittgerät“) wurde zwischenzeitlich begonnen.“
Aktualisierung und Optimierung
Historisch bedingt hatten die bisherigen Normen zum Teil recht unterschiedliche Nummern. Sie reichen von „ISO 3274:1996-12 Messgeräte” über „ISO 4287:1997-04 Kenngrößen“ bis zu „ISO 4288:1996-08 Messbedingungen“ – um nur einige von ihnen zu nennen. Ab sofort werden sie in der neuen DIN ISO 21920 zusammengefasst. Sie bildet damit den gesamten Prozess – von der Konstruktion über die Fertigung bis zur Qualitätskontrolle – in drei Teilen ab. So geht es im ersten Teil (ISO 21920-1) um Fertigung und Spezifikation, also „Zeichnungseintragungen“. Teil 2 (ISO 21920-2) definiert die Kenngrößen, und Teil 3 (ISO 21920-3) formuliert die Bedingungen, wie diese Kenngrößen am Ende überprüft werden.
Teil 1: Zeichnung stellt Funktionen des Bauteils sicher
Teil 1 löst die bisherige ISO 1302 ab und umfasst die Prozesse rund um die Zeichnungseintragungen, die ein Konstrukteur für die Fertigung eines Bauteils vorgibt. Wichtigste Änderung: Ab sofort ist ausschließlich die Zeichnung die Basis für die Bedingungen, mit denen ein gefertigtes Bauteil überprüft wird. „Auch wenn ein Konstrukteur etwas besonders Kompliziertes entwickelt, ist in Teil 1 definiert, wie er das Werkstück spezifizieren muss, ohne dass er Freitext hinzufügt. Auf diese Weise ist es möglich, dass allein die Spezifikation die Funktion der Komponente sicherstellt“, erläutert Heinz-Joachim Kedziora. Beispiel: Wenn man also nur die Kenngröße „Ra“ sowie einen Wert angibt, dann ist in vielen Fällen nicht sichergestellt, dass diese Angabe mit dem Funktionsverhalten des Teiles korreliert. Hier gibt es komplexere und weniger komplexe Kenngrößen. Zudem umfasst Teil 1 neue Begriffe für die Oberflächenparameter:
Begriff | Kurzzeichen | Erläuterung |
Auswertelänge | le | „evaluation length“, der Teil der Taststrecke, der ausgewertet wird; ersetzt lm bzw. ln. |
Nesting-Index | Nic, Nis | „Grenzwellenlänge“ nur für lineare Filter sinnvoll; ersetzt λc und λs |
Profil-S-Filter | Profil-S-Filter entfernt kurzwellige Anteile (Tiefpass); für Rauheitskennwerte entfernt das Nis-Filter („λs-Filter“) sehr kurzwellige Anteile, die nicht zum R-Profil gehören. Für Welligkeitskennwerte entfernt das Nic-Filter („λc-Filter“) kurzwellige Anteile, die zum R-Profil und nicht zum W-Profil gehören. | |
Profil-L-Filter | Profil-L-Filter entfernt langwellige Anteile (Hochpass); für Rauheitskennwerte entfernt das Nic-Filter („λc-Filter“) langwellige Anteile, die nicht zum R-Profil gehören. | |
Abschnittlänge | lsc | „section length“ für die Kenngrößen, die aus Profilabschnitten berechnet werden, z.B. Rz, Rp, Rv; ersetzt den Begriff „Einzelmessstrecke“ |
Anzahl Abschnitte | nsc | „number of sections“; ersetzt den Begriff „Anzahl Einzelmessstrecken“ |
Wichtig für alle Anwender: Die neue Norm gilt nur für neue Zeichnungen. Älter datierte Zeichnungen behalten ihre Gültigkeit unter der früheren Norm.
Ebenfalls neu sind einige Symbole, die eingeführt wurden, um den eindeutigen Bezug einer Zeichnung nach DIN EN ISO 21920-1 herzustellen:
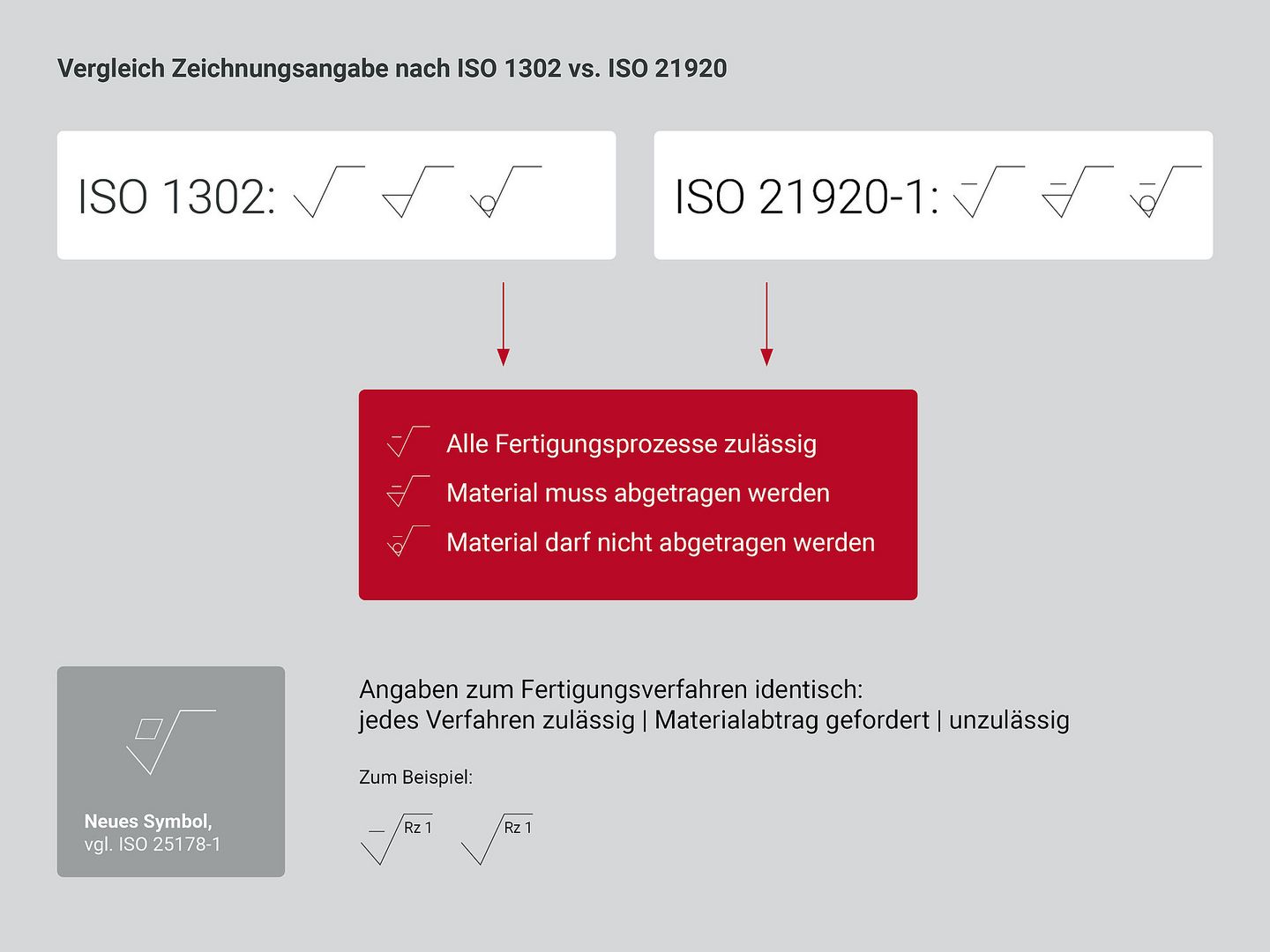
Teil 2: Konstrukteure sind gefragt
Der zweite Teil der neuen ISO 21920 beschäftigt sich mit dem Zusammenhang zwischen Kenngrößen und Funktionen von Bauteilen. Er ist der umfangreichste und wohl schwierigste Teil und ersetzt die frühere ISO 4287. „Über 100 Kenngrößen sind hier beschrieben, die den Konstrukteuren einen enormen Werkzeugkasten bieten. Sie sind künftig gefragt, aus diesem Teil die richtige Kenngröße auszuwählen. Die Auswahl fällt erfahrungsgemäß vielen Anwendern schwer, da dieses Thema keinen Ausbildungsschwerpunkt darstellt“, so der Entwicklungsleiter.
Bei den Kenngrößen, die aus Profilelementen (= ein Berg und ein Tal im Profil) berechnet werden, gab es bisher größere Messunsicherheiten, da die Profilelemente zwar beschrieben, aber im Detail, insbesondere in Grenzfällen, nicht eindeutig definiert waren. Das wurde jetzt deutlich verbessert. Die Hersteller von Messtechnik sind jedoch nicht gezwungen, all diese Kenngrößen in ein Gerät oder eine Software zu programmieren, da manche von ihnen nur regional eine Rolle spielen.
Teil 3: Wie man zu einem validen Ergebnis gelangt
Teil 3 definiert die Bedingungen, nach bzw. unter denen gemessen wird. Er ersetzt die bisherige ISO 4288 und beschäftigt sich mit dem Thema „Specification and Verification“ – also Anforderungen an Messverfahren und deren korrekte Umsetzung. Damit definiert Teil 3den Default-Fall. Das bedeutet: Wenn in der Zeichnung keine expliziten Angaben gemacht werden, gilt das, was in der Norm steht – also all das, was nicht explizit spezifiziert werden muss.
„In diesem Teil geht es also nicht nur um die Messbedingungen, sondern auch um zusätzlich zu beachtende Faktoren, wie man zu einem validen Ergebnis gelangt. Deshalb gibt es in diesem Teil keine Vorschriften, wie man etwas misst, sondern lediglich die Beschreibung eines vollständigen Spezifikationsoperators“, erklärt Kedziora. Die Spezifikation ist theoretisch ideal und eindeutig. Gemäß ISO 8015 gilt: „Der Verifikationsoperator ist die physikalische Implementierung des Spezifikationsoperators. Er kann genau dieselben Operationen in derselben Reihenfolge besitzen (in diesem Fall ist die Verfahrensunsicherheit gleich null) oder er kann unterschiedliche Operationen besitzen oder die Operationen in einer anderen Reihenfolge durchführen (in diesem Fall ist die Verfahrensunsicherheit nicht gleich null).“
Für die Verifikation gibt man also lediglich die Unsicherheit an, was in der Praxis zumeist nicht einfach ist. Als Beispiel sei die Verwendung des Gauß-Filters betrachtet: Wenn im Standardfall die Spezifikation von einem Profilpunktabstand von 0,5 µm ausgeht, so ist es nicht verboten, bei der Verifikation einen größeren oder kleineren Punktabstand zu verwenden; der Anwender muss dieses dann bei der Abschätzung der Messunsicherheit berücksichtigen.
Fazit: Erweiterte Möglichkeiten der Funktionsbeschreibungen
Für die meisten Anwender ändert sich mit der neuen Norm überhaupt nichts. Sie bietet nur erweiterte Möglichkeiten der Funktionsbeschreibung, etwa bei additiven Fertigungsverfahren, bei denen z. T. neue Strukturen oder neue Filter benötigt werden.
Anders als früher bestimmt nicht mehr das Werkstück die Filtereinstellung, sondern die dazugehörige Zeichnung. Dadurch wird die Zuverlässigkeit der Entscheidung erhöht, ob die geprüfte Oberfläche die Anforderungen erfüllt oder nicht. Es entfällt das gemäß DIN EN ISO 4288 aufwändige – und in der Praxis kaum beachtete – Verfahren zur Prüfung einer Werkstückoberfläche einschließlich der subjektiven Beurteilung, ob ein Profil periodisch oder aperiodisch ist.
Insgesamt wurde bei der neuen Norm ein großer Wert auf Kontinuität gelegt. „Unterm Strich kann man sagen: Die Schwachstellen der alten Norm – etwa unsaubere und nicht-praktikable Definitionen – sind entfallen. Dort, wo die alte Norm vernünftige Ergebnisse geliefert hat, gilt dies auch für die neue Norm. Dort, wo die alte Norm unscharf war, ist die neue Norm schärfer“, resümiert Entwicklungsleiter Kedziora. „Aufgrund der Kontinuität, durch die in der neuen Profilnorm alles beibehalten wurde, was sich in der industriellen Praxis bewährt hat, können Anwender auch mit ihren bereits vorhandenen Messgeräten weiterhin normgerecht messen.“
Derzeit erstellt das Deutschen Institut für Normung e. V. (DIN) die nationalen Normen DIN EN ISO 21920-1, -2 und -3. Es wird dringend empfohlen, die als frühe Entwürfe bereits im Jahr 2020 veröffentlichten Ausgaben DIN EN ISO 21920-1, -2 und -3 aus dem Verkehr zu ziehen, da es in der internationalen Diskussion bis zur finalen Version der Normreihe noch Änderungen gab.
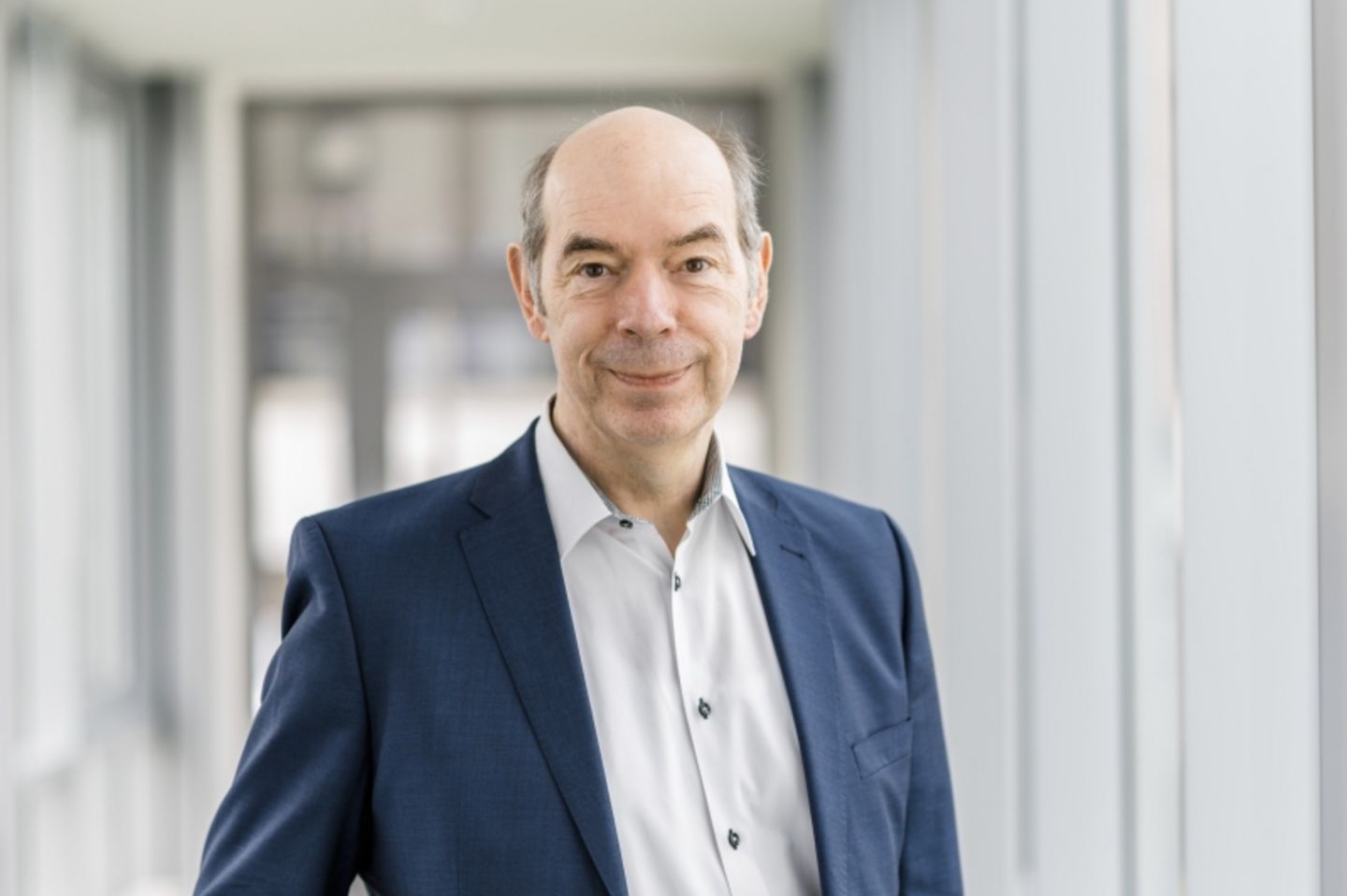
Tipp:
Unter dem Namen „Neue Oberflächennorm“ widmet Mahr ein umfassendes Webinar der neuen ISO 21920. Anschaulich und ausführlich wird erklärt, was die neue Norm für Messtechniker und Anwender bereithält. > Seminar ansehen
Die Änderungen auf einen Blick:
- Wenige neue Begriffe
- Neues Symbol für die Spezifikation
- Die Default-Toleranzakzeptanzregel ist die Höchstwert-Regel („max.-Regel“).
- Die Regelwerte basieren auf der Spezifikation (Zeichnungseintragung) und nicht auf Schätzwerten der spezifizierten Kenngröße. Dadurch ist die Zuordnung Nesting-Index abhängig vom spezifizierten Ra-bzw. Rz-Wert etwas verschoben.
- Wenn nichts anderes spezifiziert ist, erfolgt die Verifikation an dem Ort des spezifizierten Geometrieelements, an dem die Höchstwerte zu erwarten sind; Unvollkommenheiten wie z.B. Kratzer oder Poren müssen einbezogen werden.
- Keine Unterscheidung zwischen periodischen und aperiodischen Profilen
- Kennwerte sind (bis auf wenige Ausnahmen) über die Auswertestrecke definiert.
- Nur wenige Kennwerte, z.B. Rz, Rp, Rv sind über Profilabschnitte definiert (der Begriff „sampling length“ bzw. „Einzelmessstrecke“ wird nicht mehr verwendet).
- Die Spezifikation der Toleranzgrenze erfolgt unmittelbar nach der Kennwertbezeichnung.
- Vereinfachte Schreibweise zur Spezifikation von bilateralen Toleranzgrenzen
- Eine dritte Toleranzakzeptanzregel: „Tmed“: Der Medianwert aller Messwerte muss innerhalb der spezifizierten Toleranzgrenzen liegen.
- Die Spezifikation von optischen Verfahren zur Profilerfassung ist möglich, z.B. EP OR(1).