3 profesjonalne porady: Oto jak działa pomiar kształtu
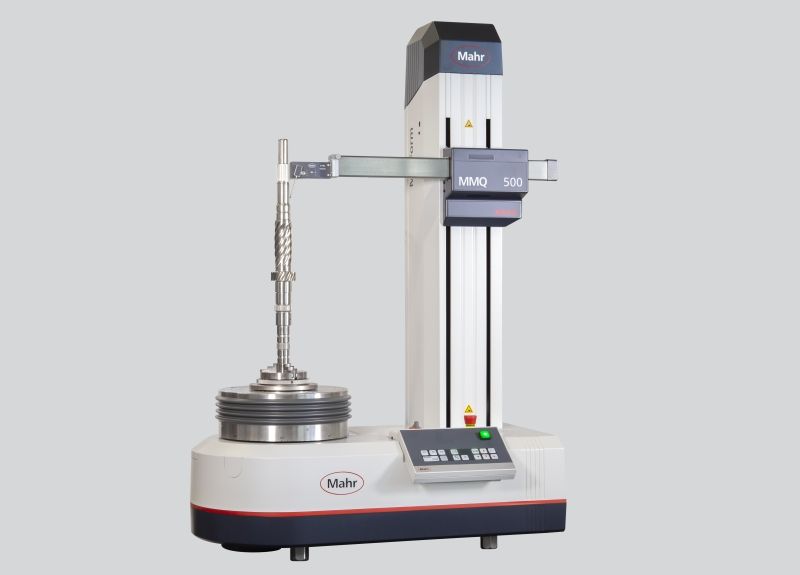
Wskazówka 1: Stosowanie odpowiednich filtrów
Aby umożliwić prawidłową ocenę danych pomiarowych, konieczny jest wybór właściwych filtrów w oprogramowaniu. Jeśli jednak ani norma zakładowa, ani klient nie podają tych ustawień filtra, zalecamy następujące postępowanie: Najpierw należy zdecydować, jakie zadanie pomiarowe ma być wykonane za pomocą maszyny do pomiaru kształtu – badanie chropowatości powierzchni czy pomiar kształtu. Następnie, w uproszczeniu: Aby sprawdzić chropowatość powierzchni detalu, należy użyć danych o krótkiej fali do analizy, odrzucając dane o długiej fali. Odwrotnie jest w przypadku pomiaru kształtu: Filtruje się i ocenia dane o długiej fali, które odnoszą się do kształtu, a odrzuca dane o krótkiej fali.
Istnieją jednak dalsze różnice pomiędzy dwoma opisanymi zadaniami pomiarowymi. Aby zmierzyć chropowatość powierzchni, należy zdefiniować ustawienia filtra w milimetrach lub calach. Na przykład, jeśli ustawi się filtr na 0,8 mm, oznacza to, że odchylenia powierzchni mniejsze niż 0,8 mm są akceptowane jako chropowatość powierzchni, podczas gdy elementy większe niż 0,8 mm nie są uwzględniane w wyniku.
Z kolei filtry kształtu, na przykład do pomiaru okrągłości, są zwykle określane jako wielkość kątowa, ale nie w stopniach kątowych, tylko w jednostce znanej jako „fale na obrót” lub w skrócie F/O (ang.: UPR). Wielu użytkowników wybiera 50 F/O jako wartość domyślną. Oznacza to, że długość łuku wynosi 1/50 okręgu lub odcinka na powierzchni okrągłego obiektu, co odpowiada 7,2 stopniom. Długość łuku zmienia się jednak analogicznie do średnicy elementu mierzonego.
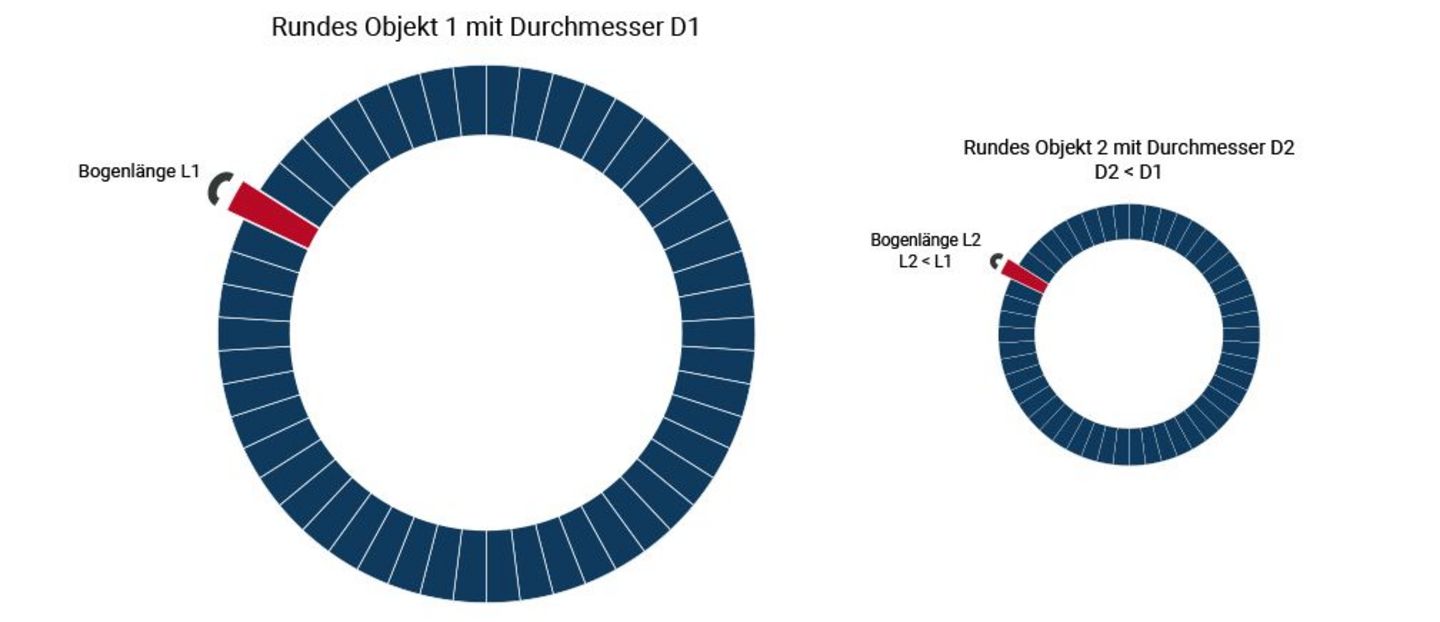
Dlatego należy zawsze dobierać odpowiedni filtr w zależności od średnicy i późniejszej funkcji obrabianego przedmiotu. W zależności od wyboru filtra, wady kształtu mogą zawierać tylko zgrubne informacje (przedmiot jest owalny lub „trójgraniasty”) lub również informacje szczegółowe, takie jak falistość o wyższej częstotliwości.
Dalsze wskazówki dotyczące właściwego doboru filtra w zależności od średnicy i zastosowania można uzyskać na przykład na szkoleniach w Mahr Academy lub podczas sesji szkoleniowej bezpośrednio na formtesterze Mahr.
Wskazówka 2: Wybrać odpowiedni rozmiar elementu stykowego
Przy wyborze elementu stykowego należy również wziąć pod uwagę wymiary badanego elementu. Dzieje się tak dlatego, że kulka stykowa jako końcówka elementu stykowego jest sama w sobie filtrem mechanicznym. Element stykowy musi zatem odpowiadać wielkości elementu mierzonego i maksymalnej mierzalnej liczbie fal na obrót. Jeżeli zbyt duży element stykowy przesuwa się po powierzchni pomiarowej, nie może optymalnie zagłębić się we wszystkie doliny profilu rzeczywistego. W wyniku tego nieodpowiedni element stykowy powoduje niezamierzone mechaniczne filtrowanie danych, które fałszuje wyniki pomiarów.
W kwestii kryteriów wyboru właściwego elementu pomiarowego może doradzić VDI/VDE-Gesellschaft Mess- und Automatisierungstechnik: Jego wytyczne VDI/VDE 2631 „Podstawy pomiaru kształtu” arkusz 3 zawierają reguły dotyczące stosowania właściwego elementu stykowego. MarForm MMQ 500 sprawia, że zastosowanie właściwego elementu stykowego jest bardzo proste: Jednostka ramienia pomiarowego mieści do czterech ramion pomiarowych jednocześnie i zmienia je szybko i w pełni automatycznie w zależności od zadania pomiarowego, bez konieczności interwencji operatora.
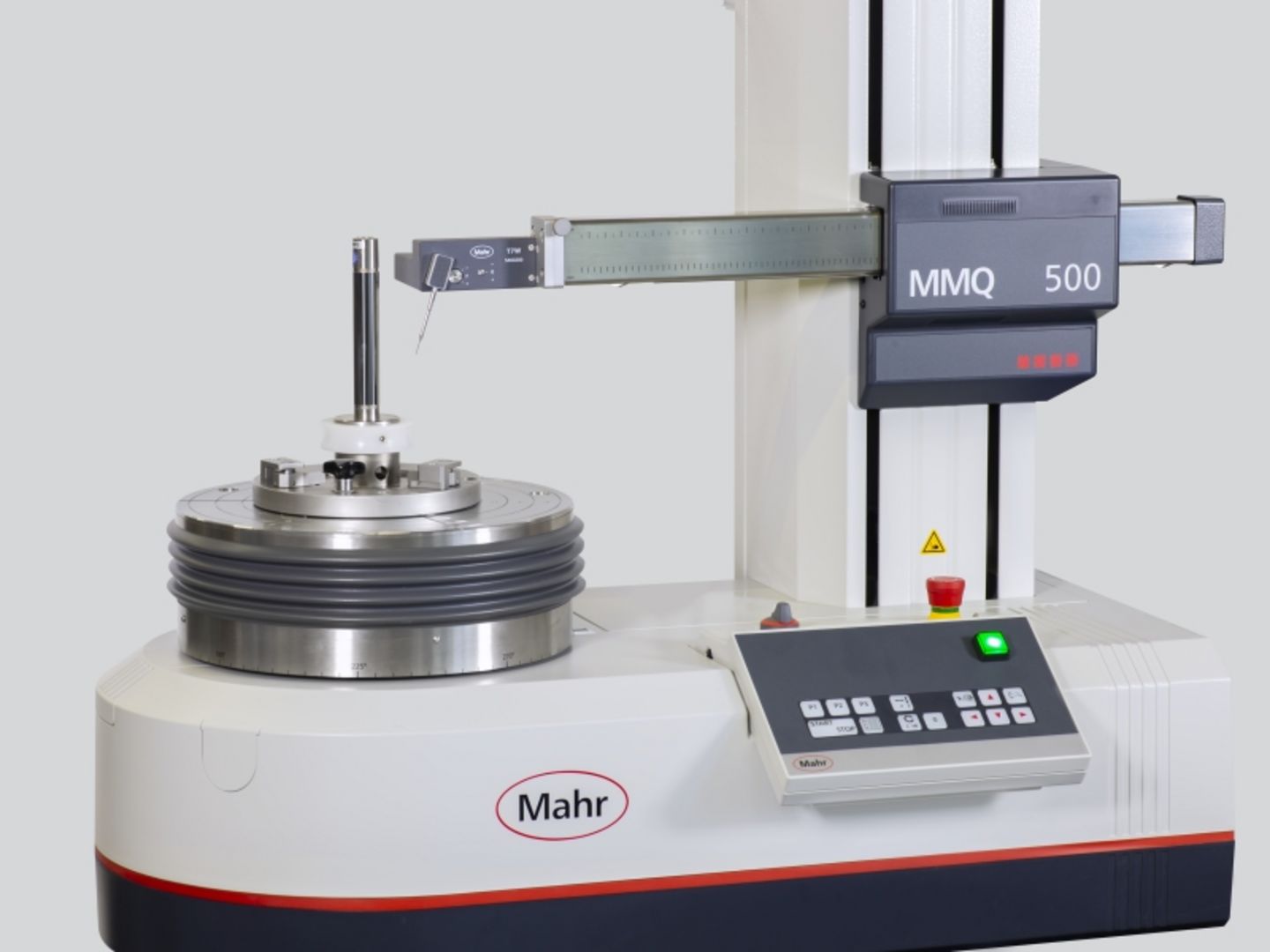
Wskazówka 3: Dokładnie wyrównać obrabiany element
Zanim będzie można zmierzyć charakterystykę kształtu i położenia detalu za pomocą formtestera, należy go najpierw wyrównać: Korzystając ze stołu centrująco-wychylnego, przechylić i wyśrodkować tak, aby oś mierzonego elementu i oś obrotu formtestera formy były w jednej linii. W ten sposób uniknie się pomiaru rzekomych błędów kształtu, które w rzeczywistości nie występują. Na przykład, w przypadku niewłaściwego wyrównania, przekrój przez walec ukośny może być błędnie wyświetlany jako elipsa, a nie jako okrąg. Ponadto, prawidłowe zestrojenie zapobiega przemieszczaniu się punktu pomiarowego, który w idealnym przypadku leży dokładnie w płaszczyźnie X-Z, podczas pomiaru.
W przypadku formtesterów, które posiadają automatyczny stół centrująco-wychylny, jak MarForm MMQ 500, można bardzo dobrze kontrolować błędy centrowania: Ze względu na wysoką precyzję podczas centrowania, można pominąć udział błędów w pomiarach okrągłości. Na przykład, typowa pozostała mimośrodowość 5 µm dla cylindra o średnicy zewnętrznej 50 mm prowadzi do dodatkowej odchyłki okrągłości mniejszej niż jeden nanometr. W przypadku innych cech, szczególnie tych dotyczących położenia, lub elementów o małych średnicach, wpływ błędów osiowania może być większy. Jednak i w tym przypadku, dzięki dokładnemu wyrównaniu, można utrzymać tę wartość na pomijalnie niskim poziomie.
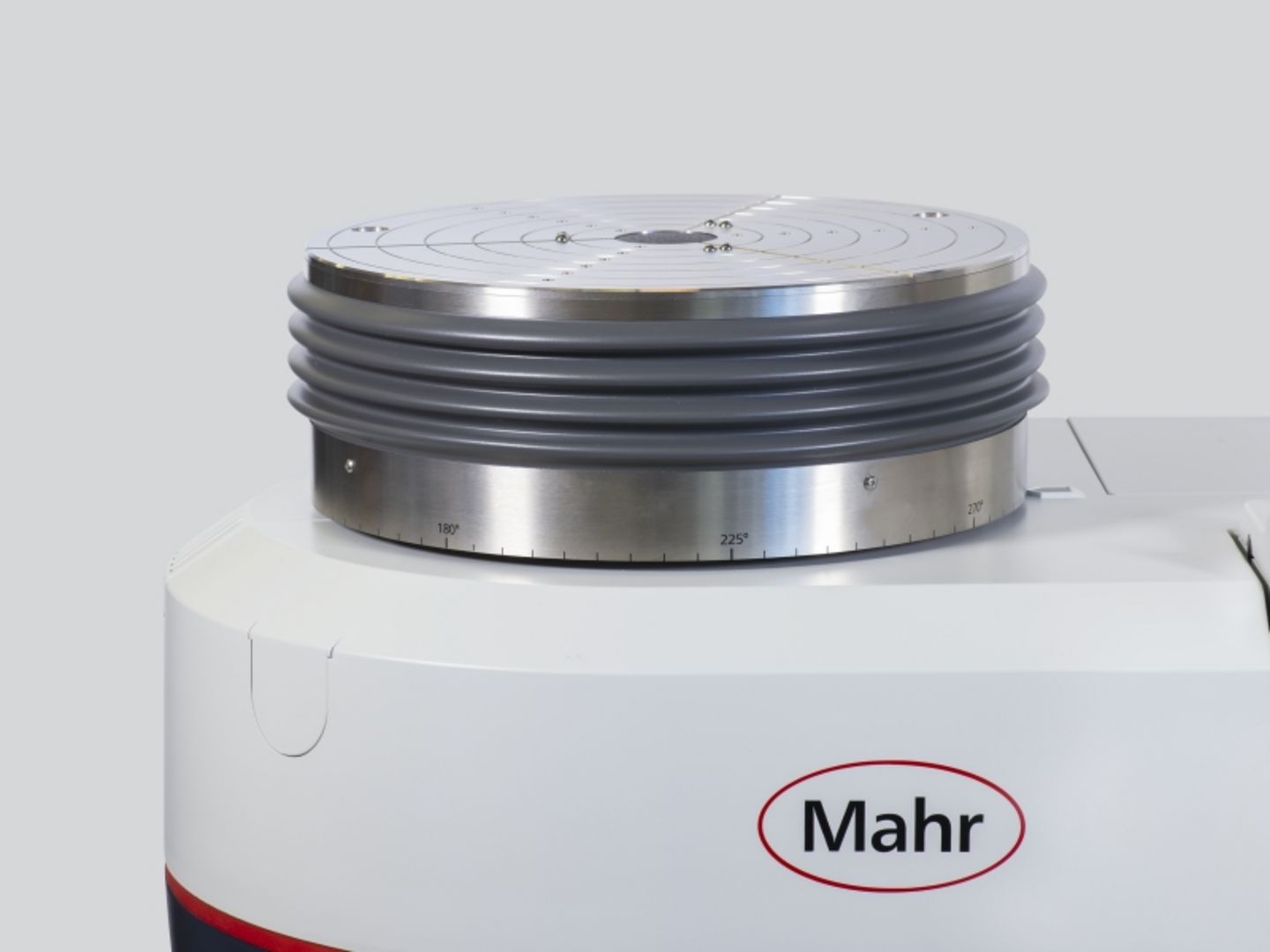
W praktyce zatem przy wyrównywaniu pojawiają się dwa podstawowe pytania:
1. Gdzie, tzn. w jakich punktach na obrabianym przedmiocie, należy dokonać wyrównania?
2. Jak dokładnie należy wyrównać obrabiany element?
Jeśli obrabiany przedmiot posiada główny punkt odniesienia (bazę), to należy go zawsze wyrównać względem niego. Jeśli nie ma głównego punktu odniesienia, sensowne jest wyrównanie w punktach o najmniejszych tolerancjach. Zaleca się ograniczenie wychylenia do dziesięciokrotności wartości liczbowej pozostałej mimośrodowości (pozostała mimośrodowość 5 µm = 50 µm/m dopuszczalnego wychylenia). Wtedy nie ma problemów z pozostałym ustawieniem skośnym, niezależnie od odległości między mierzonymi okręgami.
Dla wielu zadań pomiarowych całkowicie wystarczająca jest pozostała mimośrodowość 5 µm, zapisana jako wartość standardowa w oprogramowaniu MarWin. Formtestery Mahr zazwyczaj osiągają ją szybko i niezawodnie, więc nie należy używać większych wartości. W przypadku małych tolerancji (np. okrągłość 1 µm, cylindryczność 5 µm lub bicie poprzeczne 5 µm) lub w przypadku elementów o małych średnicach (10 mm i mniejszych) zaleca się zmniejszenie dopuszczalnej pozostałej mimośrodowości. Dzięki nowej maszynie do badania kształtu MarForm MMQ 500 można niezawodnie i szybko ustawiać elementy, nawet przy najmniejszej pozostałej mimośrodowości.