3 profesionální tipy: Takto se měření tvaru podaří
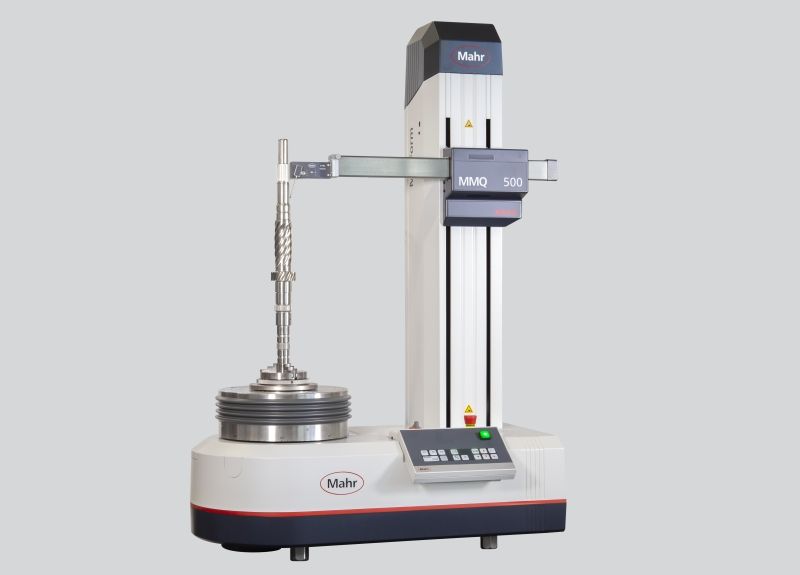
Rada 1: používejte správné filtry
Abyste mohli správně vyhodnotit naměřená data, je výběr správných filtrů v softwaru nezbytným předpokladem. Pokud však tato nastavení filtru neurčí ani interní standard ani zákazník, doporučujeme následující: Nejprve se rozhodněte, kterou měřicí úlohu byste chtěli přístrojem na měření tvarů provádět - zkoušku drsnosti povrchu nebo měření tvaru. Protože zjednodušeně platí: Pokud chcete zkontrolovat drsnost povrchu obrobku, použijete pro analýzu data s krátkou vlnovou délkou, zatímco data s dlouhou vlnovou délkou zahodíte. U měření tvaru platí opak: Data s dlouhou vlnovou délkou, která se týkají tvaru, vyfiltrujete a vyhodnotíte, data s krátkou vlnovou délkou nikoli.
Mezi oběma popsanými úlohami měření jsou však další rozdíly. Pro měření drsnosti povrchu jsou nastavení filtru definována v milimetrech nebo palcích. Pokud například nastavíte filtr na 0,8 mm, znamená to, že povrchové odchylky menší než 0,8 mm jsou považovány za drsnost povrchu, zatímco prvky větší než 0,8 mm nejsou do výsledku zahrnuty.
Na druhé straně například tvarové filtry pro měření kruhovitosti jsou obvykle uváděny jako veličina úhlu, avšak ne v úhlových stupních, nýbrž v jednotce zvané „vlny na otáčku“ neboli zkráceně v/ot (angl.: UPR). Mnoho uživatelů volí 50 v/ot jako výchozí hodnotu. To znamená, že délka oblouku je 1/50 kruhu nebo úseku na povrchu kulatého předmětu, což odpovídá hodnotě 7,2 stupně. Délka oblouku se však mění analogicky k průměru obrobku.
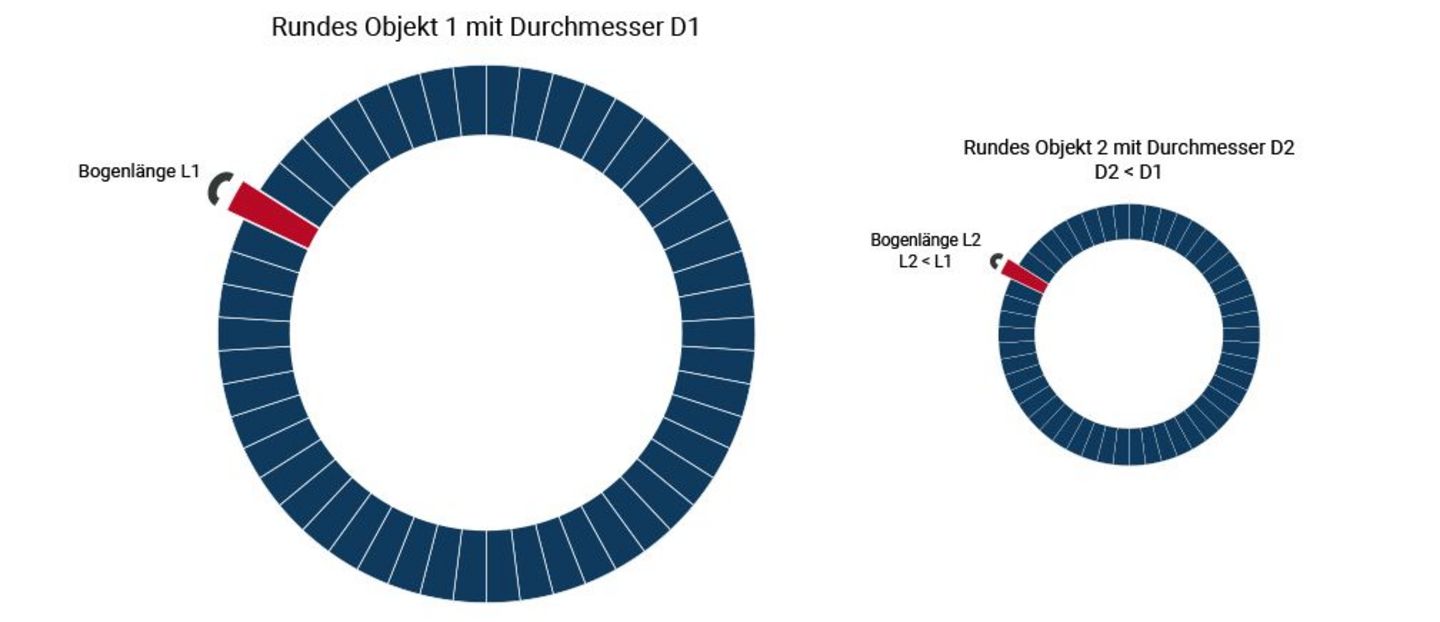
Vždy tedy musíte zvolit správný filtr v závislosti na průměru a pozdější funkci obrobku. Podle volby filtru mohou chyby tvaru obsahovat pouze hrubé podíly (obrobek je oválný nebo „třístranně stejné tloušťky“) nebo i jemnější podíly, jako je např. vlnitost vyšších frekvencí.
Další rady pro výběr správného filtru v závislosti na průměru a použití získáte například na školeních v Mahr Academy nebo během školení přímo na vašem testeru na kontrolu tvarů Mahr.
Rada 2: vyberte správnou velikost snímacího elementu
Při výběru snímacího prvku musíte také vzít v úvahu rozměry testované součásti. Protože doteková kulička jako hrot snímacího prvku je sama o sobě mechanickým filtrem. Snímací prvek proto musí odpovídat velikosti obrobku a maximálnímu měřitelnému počtu vln na otáčku. Pokud se po měřicí ploše pohybuje příliš velký snímací prvek, nemůže se optimálně ponořit do všech úžlabin reálného profilu. V důsledku toho nevhodný snímací prvek způsobí nežádoucí mechanické filtrování dat, což zfalšuje výsledky měření.
Společnost VDI/VDE pro měřicí a automatizační techniku vám ostatně poradí s kritérii výběru správného snímacího prvku: Její směrnice VDI/VDE 2631 „Základy techniky měření tvaru“, list 3, obsahuje pokyny pro použití správného snímacího prvku. Se zařízením MarForm MMQ 500 lze použití správného snímacího prvku zvládnout velmi snadno: Jeho jednotka snímacího ramena pojme až čtyři snímací ramena a mění je rychle a plně automaticky podle úlohy měření a bez jakéhokoliv zásahu obsluhy.
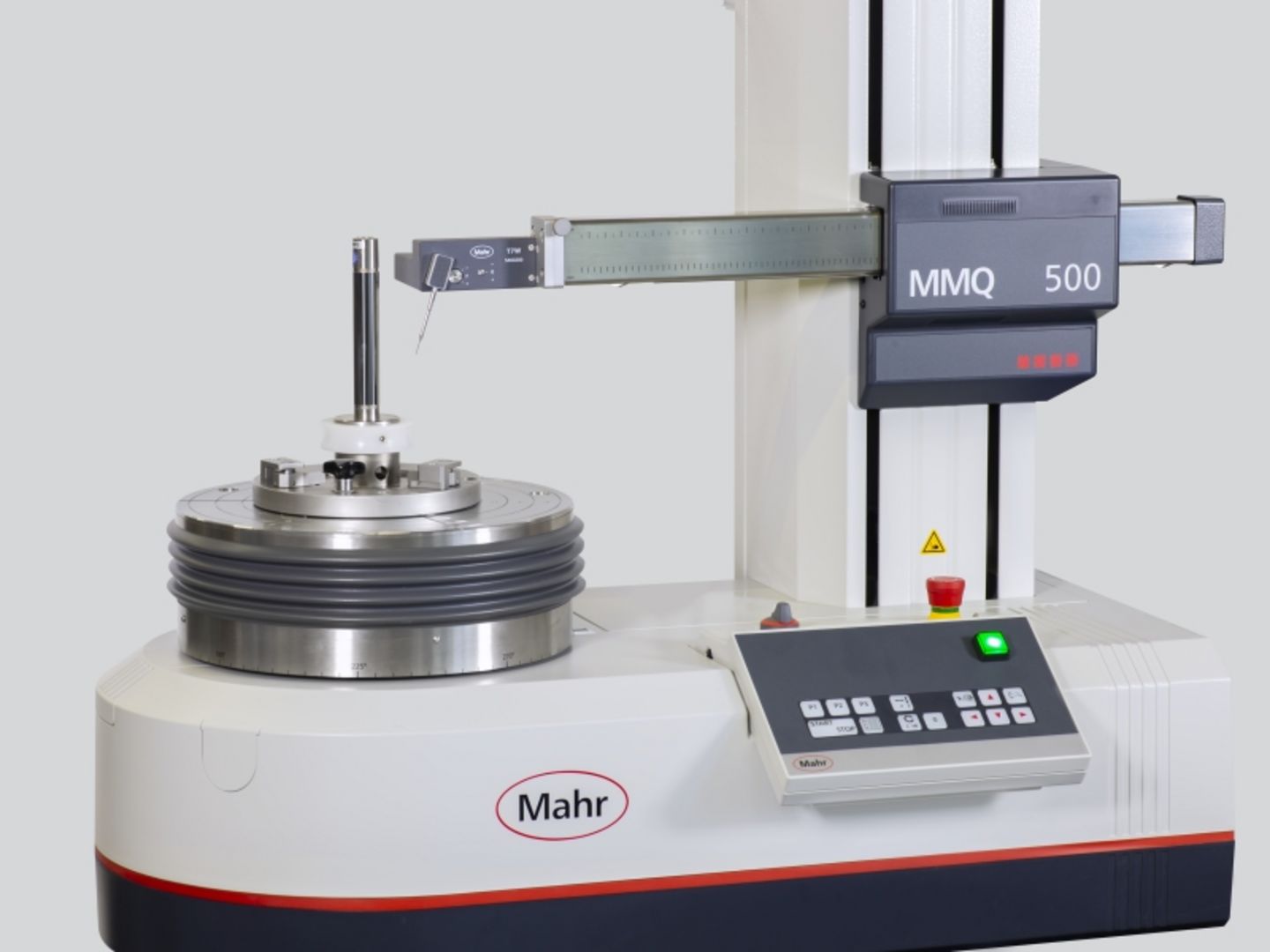
Rada 3: přesné vyrovnání obrobku
Než budete moci použít tester na kontrolu tvarů k měření charakteristik tvaru a polohy obrobku, musíte jej nejprve vyrovnat: Pomocí naklápěcího a středicího stolu jej nakloňte a vycentrujte tak, aby se osa obrobku a osa otáčení testeru na kontrolu tvarů shodovaly. To vám zabrání v měření údajných chyb tvaru, které ani neexistují. Pokud je vyrovnání nesprávné, může se například řez šikmým válcem nesprávně jevit jako elipsa, nikoli jako kruh. Správné vyrovnání navíc zabrání tomu, aby se dotykový bod, který ideálně leží přesně v rovině X-Z, během měření pohyboval.
S testery na kontrolu tvarů, které mají stejně jako MarForm MMQ 500 automatický naklápěcí a centrovací stůl, můžete velmi dobře zkontrolovat chyby vyrovnání: Vzhledem k vysoké přesnosti při vyrovnání můžete zanedbat příspěvky k chybám při měření kruhovitosti. Například typický zbývající excentr 5 µm u válce s vnějším průměrem 50 mm vede k další odchylce kruhovitosti menší než jeden nanometr. V případě jiných znaků, zejména těch týkajících se polohy, nebo součástí s malým průměrem, může být vliv chyb vyrovnání větší. I zde však platí, že ho přesným vyrovnáním můžete udržet zanedbatelně malý.
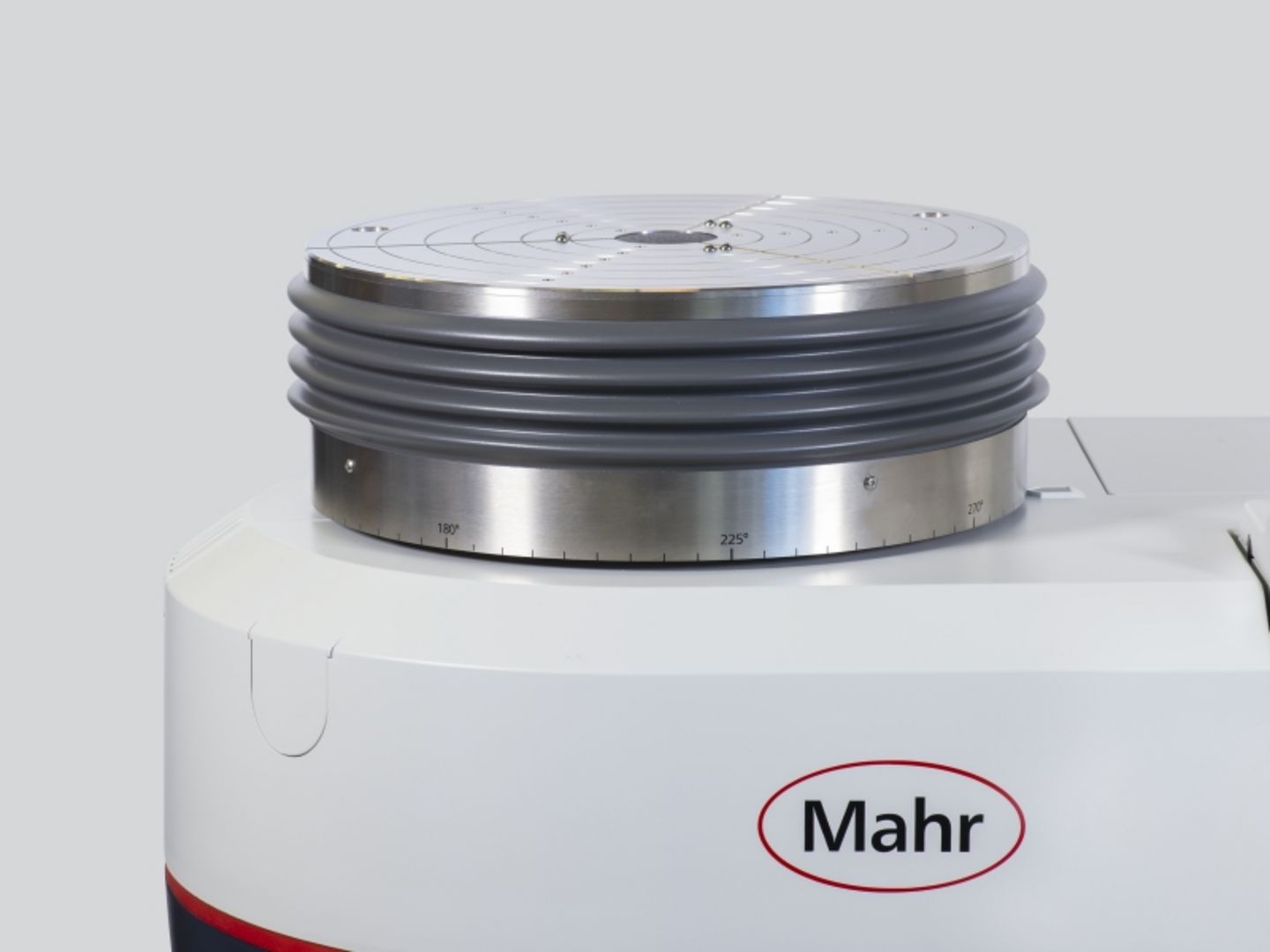
V praxi proto při vyrovnání vyvstávají v zásadě dvě otázky:
1. Kde, tj. ve kterých bodech obrobku, se musí vyrovnávat?
2. Jak přesně se obrobek musí vyrovnat?
Pokud má obrobek hlavní referenci, měli byste jej vždy vyrovnat s ní. Pokud není hlavní reference, má smysl vyrovnávat v bodech s nejmenšími tolerancemi. Doporučujeme zásadně omezit sklon na desetinásobek číselné hodnoty zbývajícího excentru (zbývající excentr 5 µm na 50 µm/m povoleného sklonu). Pak ze zbývajícího sklonu nevznikají žádné problémy, bez ohledu na vzdálenost měřených kruhů.
Zbývající excentr 5 µm uložený jako standardní hodnota v softwaru MarWin je naprosto dostačující pro mnoho měřicích úloh. Testery na kontrolu tvarů společnosti Mahr ho obvykle dosahují rychle a spolehlivě, proto byste neměli používat větší hodnoty. V případě malých tolerancí (např. kruhovitost 1 µm, tvar válce 5 µm nebo soustřednost 5 µm) nebo u součástí s malým průměrem (10 mm a menším) se doporučuje povolený zbývající excentr snížit. S novým testovacím přístrojem na kontrolu tvarů MarForm MMQ 500 můžete rychle a bezpečně vyrovnat součásti i na nejmenší zbývající excentr.